One stop supplier of water treatment parts&accessories
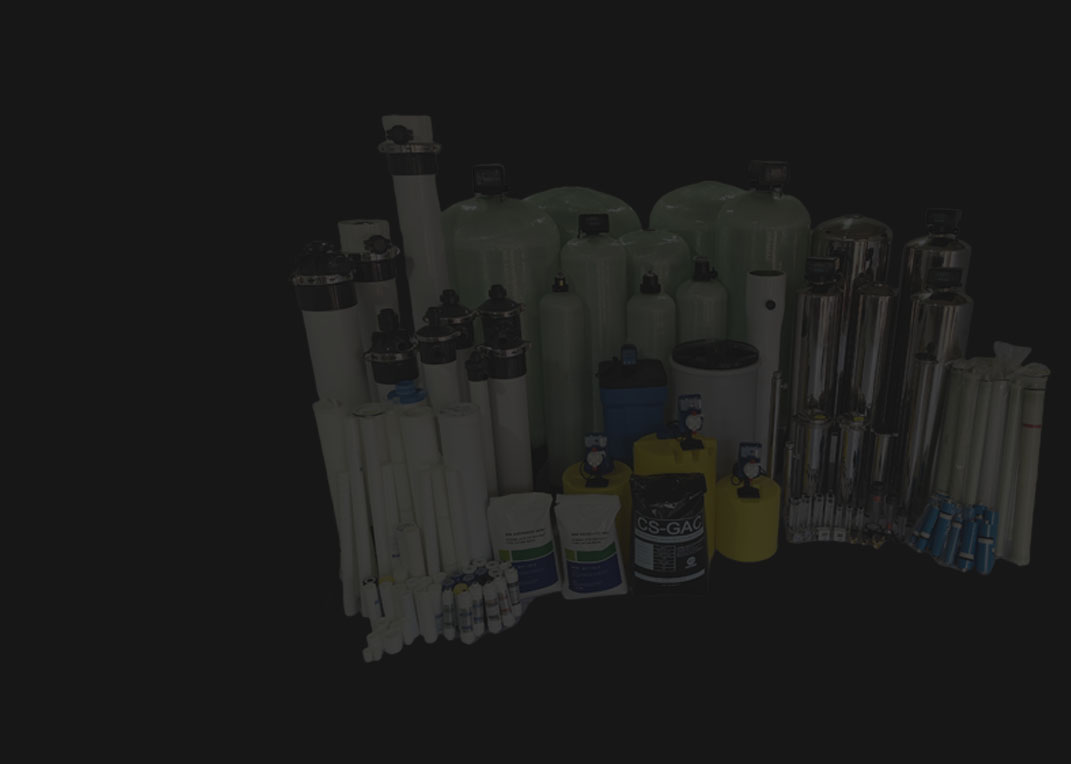
Mastering the Power of pH Controller with Dosing Pump: A Comprehensive Guide
In the intricate landscapes of industrial operations, water treatment facilities, and even home – based aquariums, operators and enthusiasts rely heavily on a pH controller with a dosing pump. This dynamic duo has become an essential asset for maintaining the delicate balance of pH levels, which is crucial for the success and efficiency of various processes. Manufacturers engineer these systems with precision and innovation to meet the diverse needs of different applications.
1. Understanding the Significance of pH Control
1.1 pH in Industrial Applications
In industries like textile manufacturing, the pH of the dye bath can significantly impact the quality of the final product. Operators use a pH controller with a dosing pump to precisely add acids or alkalis. For instance, when dyeing cotton fabrics, maintaining the right pH ensures uniform color absorption. By carefully adjusting the pH, textile workers can enhance the colorfastness and vibrancy of the dyed materials, reducing the likelihood of costly re – dyeing processes.
In the food and beverage industry, pH control is non – negotiable for food safety and flavor preservation. Brewers, for example, need to regulate the pH during the brewing process to ensure proper yeast fermentation. They rely on a pH controller with a dosing pump to add buffering agents at the right time and in the correct amounts. This helps in producing beer with consistent taste and quality, meeting consumer expectations.
1.2 pH in Water Treatment
Water treatment professionals play a crucial role in safeguarding the quality of our water sources. A pH controller with a dosing pump is their trusted ally. When treating raw water, they use this system to adjust the pH to a suitable level for further treatment. If the incoming water is too acidic, they add lime using the dosing pump, under the guidance of the pH controller. This adjustment ensures that the water is ready for disinfection and filtration processes, making it safe for consumption or industrial use.
In wastewater treatment, maintaining the right pH is essential for the effectiveness of biological treatment processes. Bacteria that break down organic matter in wastewater thrive within a specific pH range. Operators use a pH controller with a dosing pump to add chemicals that keep the pH in the optimal range, enhancing the efficiency of wastewater treatment plants.
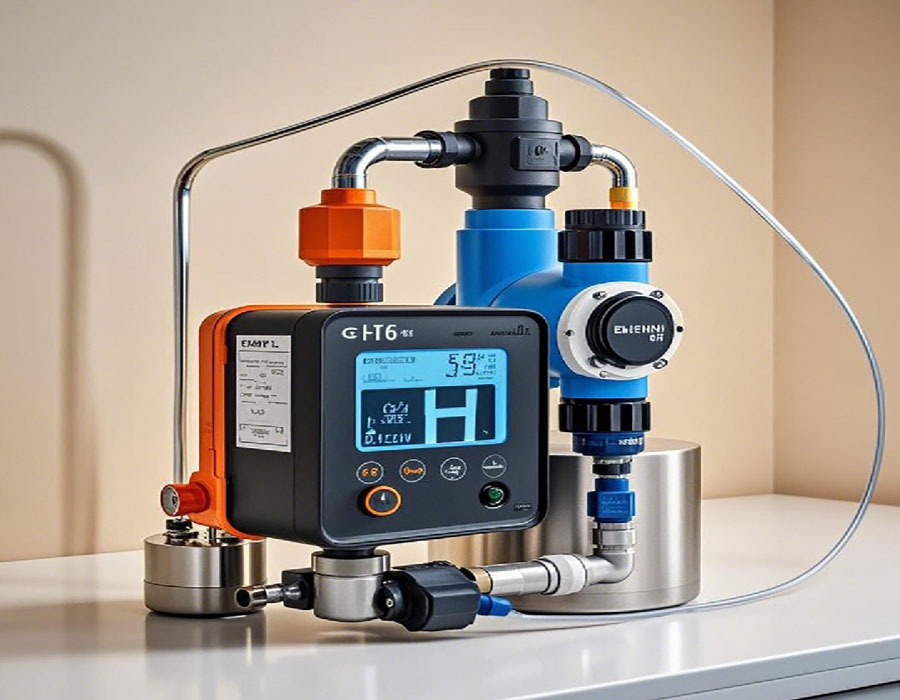
2. How a pH Controller with Dosing Pump Works
2.1 The Inner Workings of the pH Controller
A pH controller operates based on a fundamental principle. It houses a pH sensor, typically a glass electrode. This sensor measures the hydrogen ion concentration in the solution. As it does so, it generates an electrical signal that corresponds to the pH value. The controller unit then receives this signal. It compares the measured pH value against a pre – set target pH value that the operator has inputted. If there’s a deviation, the controller calculates the necessary corrective action.
2.2 The Function of the Dosing Pump
Once the pH controller determines that a pH adjustment is needed, it activates the dosing pump. The dosing pump is connected to a reservoir filled with the appropriate chemical for pH adjustment, such as an acid or a base. When activated, the pump delivers a precise amount of the chemical into the solution. For example, if the measured pH is higher than the target pH, indicating an alkaline solution, the controller signals the dosing pump to add a specific volume of acid. The pump’s flow rate and the duration of operation are carefully regulated by the pH controller to ensure a gradual and accurate pH adjustment.
3. Types of pH Controllers and Dosing Pumps
3.1 Varieties of pH Controllers
There are different types of pH controllers available on the market. Basic analog pH controllers are simple and cost – effective. Operators can use them for straightforward applications where high – precision control isn’t essential. These controllers have a display that shows the measured pH value, and operators can manually adjust the set – point and control parameters.
Digital pH controllers, on the other hand, offer enhanced accuracy and more advanced control features. They can be programmed to execute complex control algorithms, such as proportional – integral – derivative (PID) control. This type of control allows for more precise and responsive pH regulation. Some digital pH controllers also come equipped with communication interfaces, enabling remote monitoring and control. This feature is especially useful for large – scale industrial operations or for operators who need to manage their systems from a distance.
3.2 Dosing Pump Options
Diaphragm dosing pumps are a popular choice for pH control applications. They operate using a flexible diaphragm. When the pump is activated, the diaphragm flexes, creating a suction and discharge action. This design ensures that the moving parts of the pump don’t come into direct contact with the chemical being pumped. This is crucial when dealing with corrosive substances like acids and alkalis, as it helps to prevent damage to the pump and ensures the integrity of the chemical being dosed.
Piston dosing pumps are another option. They use a piston to push the liquid out of the cylinder. These pumps can handle higher pressures and larger volumes compared to diaphragm pumps. In industrial applications where a significant amount of chemical needs to be added, such as in large – scale water treatment plants, piston dosing pumps are often the preferred choice.
Peristaltic dosing pumps have a unique design that consists of a flexible tube and a set of rollers. As the rollers rotate, they squeeze the tube, creating a wave – like motion that moves the liquid through the tube. This type of pump is ideal for applications where contamination – free pumping is essential. In the pharmaceutical and food processing industries, for example, peristaltic dosing pumps are used for pH adjustment to ensure the purity of the products.
4. Installation and Setup Procedures
4.1 Installing the pH Sensor
Installing the pH sensor is a critical step. First, operators need to choose an appropriate location for the sensor. It should be placed in a position where it can accurately measure the pH of the solution. In a water treatment tank, for example, the sensor should be immersed in the water at a depth where the water is well – mixed. Once the location is determined, operators use the provided mounting brackets to carefully install the sensor. They then connect the sensor’s cable to the pH controller, making sure the connection is secure and free from interference.
4.2 Connecting the Dosing Pump
Connecting the dosing pump involves several steps. Operators first mount the pump in a suitable location near the chemical reservoir and the point of chemical addition. They connect the inlet tubing of the dosing pump to the chemical reservoir and the outlet tubing to the point where the chemical needs to be added to the solution. All tubing connections are tightened to prevent leaks. Next, they connect the dosing pump to the pH controller. They follow the manufacturer’s instructions to connect the control wires, allowing the pH controller to send signals to the dosing pump to start, stop, or adjust the flow rate.
4.3 Initial Setup and Calibration
After installation, operators need to set up and calibrate the pH controller and dosing pump. They enter the target pH value into the pH controller. They also adjust the controller’s control parameters, such as the proportional band, integral time, and derivative time (for PID – controlled controllers), according to the specific application requirements.
Calibration of the pH sensor is crucial. Operators use standard buffer solutions with known pH values to calibrate the sensor. By measuring the pH of these buffer solutions, they can verify the sensor’s accuracy and make adjustments if necessary. The dosing pump also needs calibration. This involves measuring the actual flow rate of the pump at different settings and adjusting the pump’s calibration settings to ensure accurate chemical dosing.
5. Maintenance and Troubleshooting
5.1 Regular Maintenance Practices
Regular maintenance is essential to keep the pH controller with dosing pump in optimal working condition. Operators should clean the pH sensor regularly to remove any deposits or contaminants that could affect its accuracy. They can use a mild cleaning solution and a soft brush for this purpose. They also need to check the sensor’s electrolyte level and refill it if necessary.
The dosing pump’s tubing should be inspected for any signs of wear, cracks, or blockages. If any issues are detected, the tubing should be replaced. The pump’s moving parts, such as the diaphragm or piston, should be lubricated regularly to ensure smooth operation. Operators should also clean and refill the chemical reservoir as needed, taking proper safety precautions when handling chemicals.
5.2 Common Troubleshooting
If the pH controller displays inaccurate pH values, it could be due to a dirty or malfunctioning pH sensor. In this case, operators should clean or replace the sensor. If the dosing pump fails to deliver the correct amount of chemical, it could be because of a clogged tubing, a malfunctioning pump motor, or incorrect calibration. Technicians can resolve a clogged tubing by removing and cleaning it. If the pump motor is faulty, it may need repair or replacement. Incorrect calibration can be fixed by repeating the calibration process.
Another common issue is that the pH controller may not be able to maintain the target pH. This could be due to a problem with the control algorithm, a sudden change in the solution’s chemistry, or a malfunctioning dosing pump. In such cases, operators need to check the controller’s settings, analyze the solution’s chemistry, and troubleshoot the dosing pump.
6. Applications Across Different Sectors
6.1 Aquariums and Aquaculture
In aquariums, maintaining the correct pH level is crucial for the health and well – being of fish and other aquatic organisms. Aquarists use a pH controller with a dosing pump to add buffers or other chemicals to keep the water’s pH within the appropriate range for the specific species of fish and plants in the aquarium. In aquaculture, large – scale fish farming operations rely on pH control to ensure the growth and survival of fish. A pH controller with a dosing pump helps in maintaining the water quality in fish ponds and tanks, reducing the risk of diseases and promoting healthy growth.
6.2 Agriculture
In agriculture, soil pH plays a vital role in plant growth. Farmers can use a pH controller with a dosing pump to adjust the pH of irrigation water. If the soil is too acidic or alkaline, adding the right amount of lime or other soil – amendment chemicals to the irrigation water can improve the soil’s pH and enhance nutrient availability for plants. This can lead to increased crop yields and better – quality produce.
6.3 Chemical Manufacturing
In chemical manufacturing, precise pH control is often required for chemical reactions. A pH controller with a dosing pump allows chemical manufacturers to maintain the optimal pH conditions during the production process. This ensures the efficiency and safety of the chemical reactions and the quality of the final products. For example, in the production of pharmaceuticals, the pH of the reaction mixture needs to be carefully controlled to ensure the correct formation of chemical compounds.
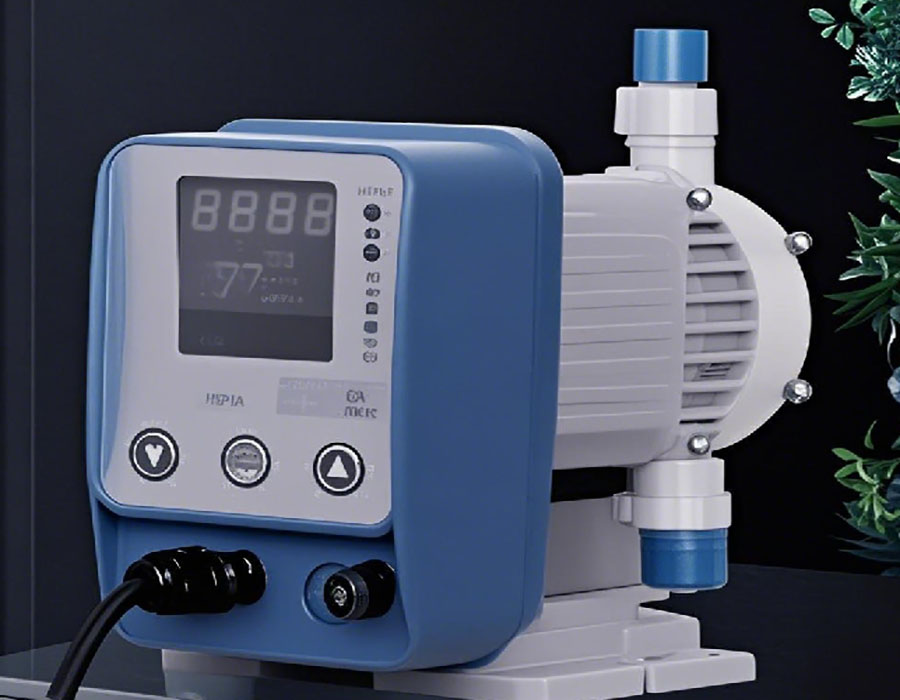
7. Selecting the Right pH Controller with Dosing Pump
7.1 Factors to Consider
When choosing a pH controller with a dosing pump, several factors come into play. The accuracy and resolution of the pH controller are crucial. For applications that demand high – precision pH control, a controller with a high – accuracy sensor and a small resolution (e.g., 0.01 pH units) is ideal. The flow rate and pressure capabilities of the dosing pump should align with the requirements of the application. If a large volume of chemical needs to be added quickly, a dosing pump with a high – flow rate and suitable pressure rating should be selected.
The compatibility of the equipment with the chemicals to be used is also important. The pH sensor and the dosing pump should be made of materials that can resist the corrosive effects of the chemicals. Additionally, the cost, ease of use, and availability of spare parts are factors that buyers should take into account.
7.2 Comparing Different Brands and Models
There are numerous brands and models of pH controllers with dosing pumps available in the market. Some brands are renowned for their high – quality sensors and reliable control systems, while others may offer more budget – friendly options. When comparing different models, buyers should consider features such as the type of control algorithm (e.g., PID or on – off control), the presence of additional features like data logging and remote monitoring, and the durability of the equipment. Reading product reviews from other users and consulting with industry experts can also aid in making an informed decision.
8. Future Prospects
8.1 Technological Advancements
The future of pH controllers with dosing pumps is likely to witness significant technological advancements. We can anticipate the development of more intelligent pH controllers with advanced sensors that can measure not only pH but also other parameters such as temperature, conductivity, and dissolved oxygen. These multi – parameter sensors will provide a more comprehensive understanding of the solution’s chemistry, enabling more precise control.
Dosing pumps may also become more efficient, with the ability to adjust the flow rate more precisely and respond more rapidly to changes in pH. Moreover, the integration of wireless communication technologies will enable remote monitoring and control of pH controllers with dosing pumps, making it more convenient for operators to manage their systems from a distance.
8.2 Environmental Considerations
With the growing focus on environmental protection, future pH control systems may be designed to be more environmentally friendly. This could involve the use of more sustainable materials in the construction of the equipment, the development of energy – efficient dosing pumps, and the reduction of chemical waste. For example, manufacturers may develop dosing pumps that can accurately dose chemicals in smaller quantities, minimizing the amount of excess chemicals that need to be disposed of.
In conclusion, a pH controller with a dosing pump is an indispensable tool in a wide range of applications. By understanding its working principle, installation, maintenance, and the factors to consider when choosing one, users can maximize its potential. Whether it’s for maintaining a small – scale aquarium or ensuring the smooth operation of a large – scale industrial process, the right pH controller with dosing pump can make a substantial difference.