One stop supplier of water treatment parts&accessories
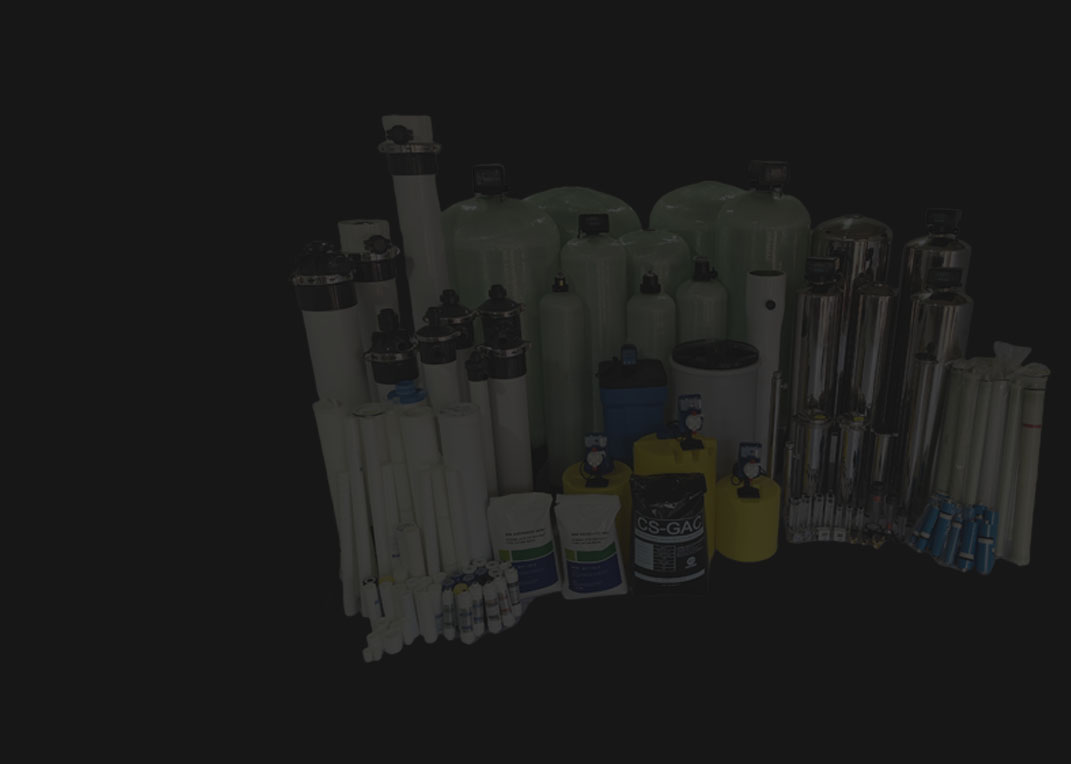
The Crucial Role and Comprehensive Exploration of Dosing Pump Chlorine
In the vast landscape of water treatment and various industrial processes, the use of a dosing pump for chlorine is of utmost importance. Chlorine, a powerful disinfectant, can eliminate harmful microorganisms in water sources effectively. Professionals carefully design and install a dosing pump chlorine system to ensure the accurate and controlled addition of , which is essential for safeguarding public health and maintaining the quality of water in numerous applications.
1. Significance of Chlorine Dosing in Water Treatment
1.1 Disinfection Process
Chlorine serves as a highly effective disinfectant in water treatment plants. When adding it to water, it reacts with and destroys bacteria, viruses, and other pathogens. Operators use a dosing pump chlorine setup to introduce precisely into the water stream. For example, in municipal water treatment, workers first filter the water to remove large particles and then employ a dosing pump to add at a specific concentration. This ensures that the water is free from harmful microorganisms when it reaches consumers’ taps. If the operators don’t add chlorine accurately, under – dosing could lead to potential health risks due to the presence of pathogens, while over – dosing might result in an unpleasant taste and odor in the water.
1.2 Maintaining Water Quality in Distribution Systems
Once the water treatment plant treats the water with chlorine, it needs to maintain its quality during distribution. Workers can install a dosing pump chlorine system at various points in the water distribution network. This ensures that a residual amount of chlorine remains in the water to prevent the regrowth of bacteria during its journey through pipes to consumers. In large – scale water supply systems, the water may travel long distances, and without proper chlorine dosing, the water could become contaminated again. The dosing pump adjusts the levels based on the water flow rate and the detected residuals, thus keeping the water safe throughout the distribution process.
2. Working Principle of Dosing Pump for Chlorine
2.1 Fundamental Operation
A dosing pump for typically operates based on either a positive – displacement or a diaphragm – based mechanism. In a positive – displacement dosing pump, a motor drives a piston or a plunger. As the piston moves within a cylinder, it creates a suction force that draws the liquid chlorine (or a chlorine – containing solution) from a storage tank through an inlet valve. When the piston moves in the opposite direction, it forces the chlorine – rich liquid out through an outlet valve. Technicians calibrate this movement to deliver a specific volume of chlorine with each stroke, allowing for precise dosing.
2.2 Control Systems
Modern dosing pumps for chlorine often come equipped with advanced control systems. Operators can program these systems to adjust the dosing rate based on various parameters. For instance, sensors can measure the flow rate of the water to be treated. If the water flow increases, the control system can automatically increase the dosing rate of the chlorine to maintain the proper chlorine – to – water ratio. Additionally, sensors can monitor the chlorine residual in the treated water. If the residual level drops below the required standard, the control system will signal the dosing pump to increase the output.
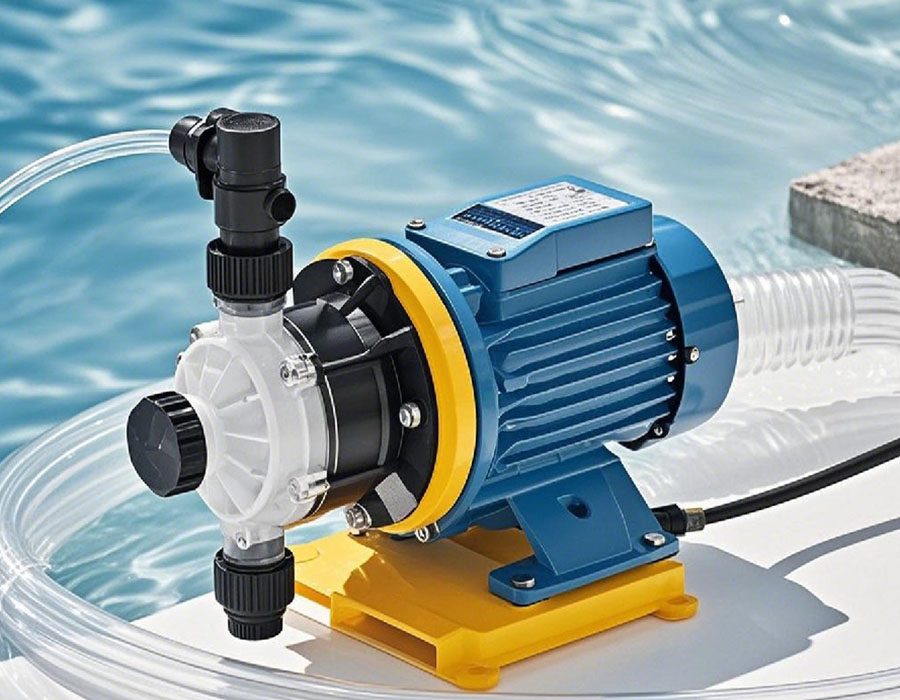
3. Types of Dosing Pumps for Chlorine
3.1 Diaphragm Dosing Pumps
Designers construct diaphragm dosing pumps with a flexible diaphragm that separates the fluid – handling chamber from the drive mechanism. When the pump activates, the diaphragm flexes, creating a suction and discharge action. This design is beneficial when dealing with chlorine, as it ensures that the moving parts of the pump are not in direct contact with the corrosive chlorine. In water treatment plants, workers often use diaphragm dosing pumps to add small to moderate amounts of chlorine accurately. They can adjust these pumps to deliver precise volumes of chlorine, making them suitable for applications where a high level of dosing accuracy is required.
3.2 Piston Dosing Pumps
Piston dosing pumps are another option for chlorine dosing. They use a piston that moves within a cylinder to pump the chlorine – containing liquid. Piston dosing pumps can handle higher pressures and larger volumes compared to diaphragm pumps in some cases. In industrial water treatment plants where a large quantity of chlorine needs to be added, piston dosing pumps can be an ideal choice. However, due to the direct contact between the piston and the cylinder walls, workers may need to maintain them more frequently to ensure smooth operation and accurate dosing.
3.3 Peristaltic Dosing Pumps
Peristaltic dosing pumps operate on a unique principle. They consist of a flexible tube and a set of rollers. As the rollers rotate, they squeeze the tube in a wave – like motion, moving the chlorine – containing liquid through the tube. This type of pump is highly suitable for applications where contamination – free pumping is essential. In swimming pool water treatment, workers often use peristaltic dosing pumps to add chlorine. The flexible tube ensures that the chlorine does not come into contact with the internal components of the pump, reducing the risk of corrosion and ensuring the purity of the chlorine being dosed.
4. Installation and Setup of Dosing Pump Chlorine Systems
4.1 Installation Process
Installing a dosing pump chlorine system requires careful planning. First, installers must select a suitable location for the dosing pump and the storage tank. The area should be well – ventilated to prevent the accumulation of chlorine gas, which can be harmful. Once they determine the location, they use the provided brackets to mount the dosing pump securely. They connect the inlet tubing to the chlorine storage tank and the outlet tubing to the point where the chlorine needs to be added to the water stream. Installers tighten all tubing connections to prevent leaks and route the tubing in a way that does not interfere with other equipment in the water treatment facility.
4.2 Initial Setup and Calibration
After installation, technicians need to set up and calibrate the dosing pump. They program the control system of the dosing pump to set the desired dosing rate. This is usually based on the water flow rate, the required chlorine concentration, and the quality of the incoming water. Calibration is a crucial step to ensure the accuracy of the dosing pump. Technicians use measuring devices, such as flow meters and chlorine analyzers, to verify the amount of chlorine being dispensed. They may need to repeat the calibration process periodically to account for any wear and tear on the pump’s components or changes in the properties of the chlorine – containing solution.
5. Maintenance and Troubleshooting of Dosing Pump Chlorine Systems
5.1 Regular Maintenance
Regular maintenance is essential to keep a dosing pump chlorine system in optimal working condition. Technicians should inspect the tubing regularly for any signs of wear, cracks, or blockages. They should clean and lubricate the pump’s moving parts, such as the diaphragm, piston, or rollers, as per the manufacturer’s instructions. They also need to inspect the chlorine storage tank for any signs of corrosion or leakage. Additionally, they should check the control system to ensure that the sensors are functioning properly and that the dosing settings are still accurate. Regular maintenance not only extends the lifespan of the dosing pump but also ensures the reliable and accurate addition of .
5.2 Common Troubleshooting
If a dosing pump fails to deliver the correct amount of , several issues could be the cause. A clogged inlet or outlet tubing can restrict the flow of chlorine. Technicians can resolve this by removing the tubing and cleaning it thoroughly. If the pump is making unusual noises, it could indicate a problem with the motor or the moving parts. In such cases, technicians may need to disassemble and inspect the pump for any signs of damage or misalignment. Another common issue is inaccurate dosing, which could be due to a malfunctioning control system or incorrect calibration. In this case, technicians should check the control system and repeat the calibration process.
6. Applications of Dosing Pump Chlorine in Different Industries
6.1 Municipal Water Treatment
In municipal water treatment plants, workers use dosing pump chlorine systems to disinfect large volumes of water. They source the water from rivers, lakes, or groundwater, first treat it to remove impurities, and then add chlorine using dosing pumps. This ensures that the water is safe for consumption by the public. Workers carefully calibrate the dosing pumps to meet the water quality standards set by regulatory authorities, providing clean and safe drinking water to the community.
6.2 Swimming Pool Maintenance
Swimming pools require regular chlorine dosing to keep the water free from bacteria and algae. Operators install a dosing pump chlorine system in swimming pools to add the appropriate amount of based on the pool’s volume, the number of swimmers, and the water temperature. This helps to maintain a clean and hygienic swimming environment, preventing the spread of water – borne diseases among swimmers.
6.3 Industrial Water Treatment
In industries such as food and beverage, pharmaceutical, and power generation, water is used in various processes. Workers use dosing pump chlorine systems to treat the incoming water to ensure that it meets the quality requirements for these processes. For example, in the food and beverage industry, the water used in production must be free from contaminants. Workers add chlorine using dosing pumps to disinfect the water, preventing the growth of bacteria that could spoil the food products or cause health issues for consumers.
7. Choosing the Right Dosing Pump for Chlorine
7.1 Factors to Consider
When choosing a dosing pump for chlorine, buyers need to consider several factors. The flow rate requirements are crucial. The dosing pump should be able to deliver the required volume of based on the volume of water to be treated. The pressure rating of the pump is also important, especially if the water treatment system has high – pressure water lines. The type of to be used, whether it is liquid gas, or a – based powder, will also influence the choice of the dosing pump. Additionally, the accuracy requirements of the dosing, the budget available for the purchase and maintenance of the pump, and the ease of use and availability of spare parts are all factors that buyers should take into account.
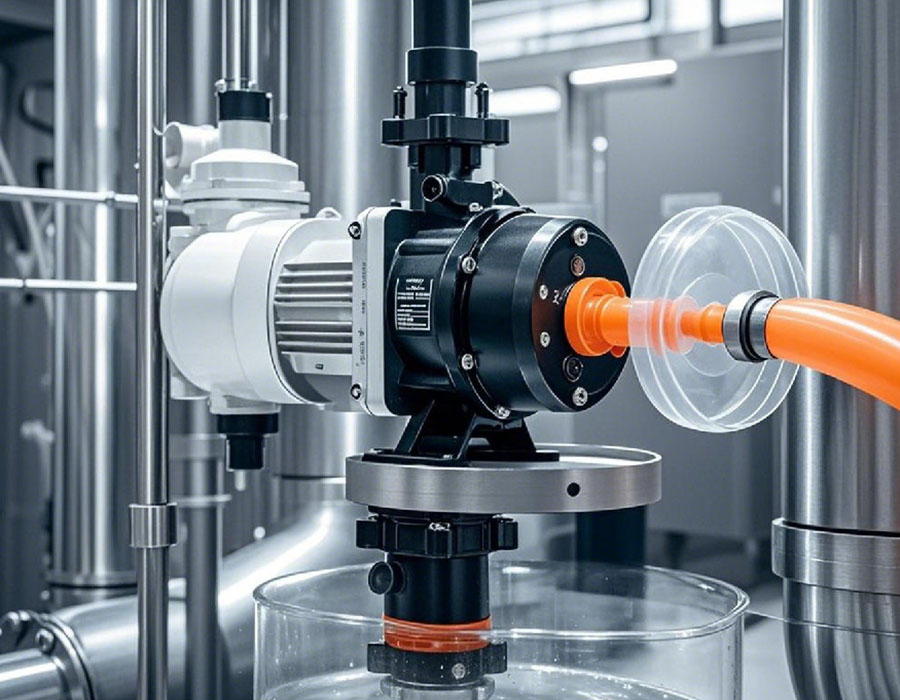
7.2 Comparing Different Brands and Models
There are numerous brands and models of dosing pumps for chlorine available in the market. Some brands are known for their high – quality construction, reliability, and accuracy. Others may offer more budget – friendly options. When comparing different brands and models, buyers should consider factors such as the pump’s performance in terms of flow rate, pressure handling, and dosing accuracy. Reading product reviews from other users and consulting with industry experts can also help buyers make an informed decision.
8. Future Developments of Dosing Pump Chlorine Systems
8.1 Technological Advancements
The future of systems is likely to see significant technological advancements. Designers may develop more intelligent dosing pumps with advanced sensors. These sensors can monitor not only the water flow rate and chlorine residual but also other parameters such as pH and temperature. The dosing pumps can then adjust the chlorine dosing automatically based on the data collected, further enhancing the efficiency and accuracy of the water treatment process.
8.2 Environmental and Safety Considerations
With the increasing focus on environmental protection and safety, future systems may feature more environmentally friendly and safer designs. For example, developers may create new materials for the construction of the pumps and the storage tanks to reduce the risk of chlorine leakage and corrosion. Additionally, they may introduce more energy – efficient operation mechanisms to reduce the power consumption of the dosing pumps.
In conclusion, the use of a dosing pump for is a critical aspect of water treatment and various industrial processes. Understanding its working principle, installation, maintenance, and the factors to consider when choosing one is essential for ensuring the effective and safe use of chlorine in these applications. Whether it’s for providing clean drinking water to a community or maintaining a hygienic swimming pool, the right dosing pump chlorine system can make a significant difference in water quality and public health.
In the vast landscape of water treatment and various industrial processes, the use of a for is of utmost importance. Chlorine, a powerful disinfectant, can eliminate harmful microorganisms in water sources effectively. Professionals carefully design and install a dosing pump chlorine system to ensure the accurate and controlled addition of , essential for safeguarding public health and maintaining the quality of water in numerous applications.