One stop supplier of water treatment parts&accessories
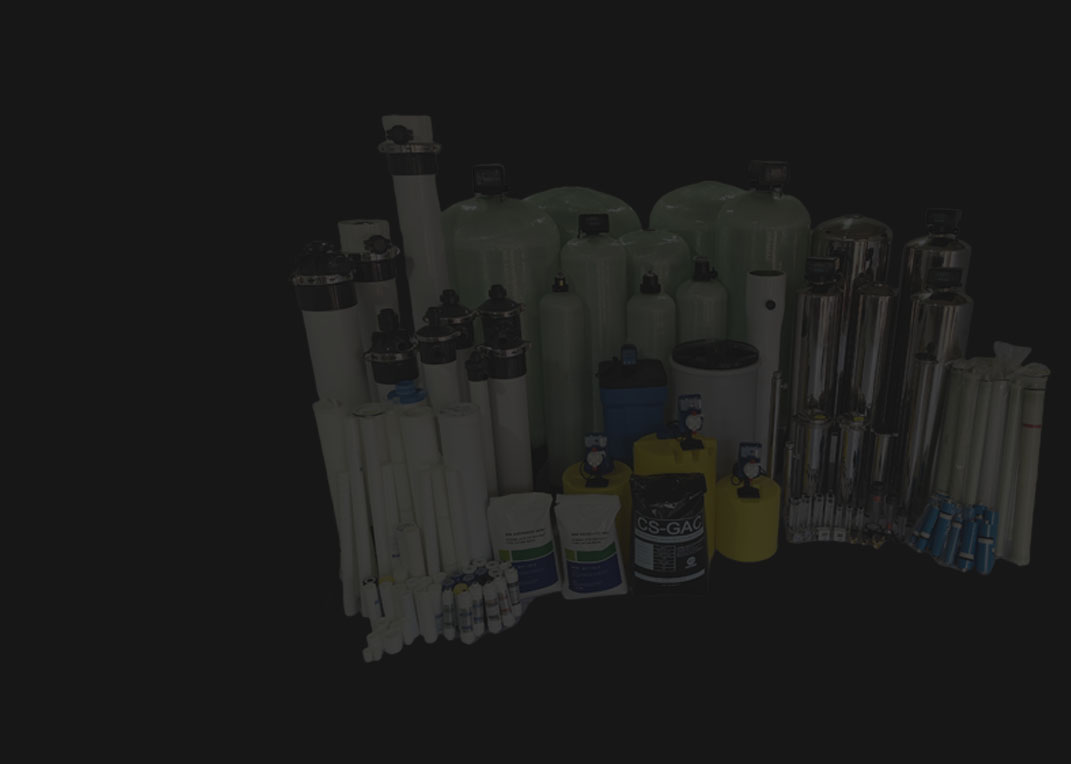
Dosing Pump Tubing: The Key Component in Precise Dosing Systems
In the world of industrial dosing systems, dosing pump tubing plays a crucial role. It’s the link that ensures the accurate transfer of various fluids from the pump to the intended process. But what exactly makes a good dosing pump tubing? And how does it impact the overall performance of the dosing system? Let’s explore these questions in detail.
What is Dosing Pump Tubing?
Dosing pump tubing is a specialized pipeline used in dosing pumps to transport liquids or chemicals precisely. It’s designed to withstand different pressures, chemical reactions, and environmental conditions. For example, in a water treatment plant, dosing pump tubing is used to deliver disinfectants accurately to the water supply.
Material Types
- PVC (Polyvinyl Chloride) Tubing: PVC tubing is widely used due to its low cost and good chemical resistance. However, it may not be suitable for high – temperature applications.
- PTFE (Polytetrafluoroethylene) Tubing: PTFE tubing offers excellent chemical resistance and can withstand high temperatures. But it’s relatively more expensive.
- Silicone Tubing: Silicone tubing is flexible and has good resistance to certain chemicals. It’s often used in food and pharmaceutical industries because of its non – toxicity.
Key Features
- Pressure Resistance: Dosing pump tubing needs to handle the pressure generated by the pump. Different materials have different pressure – bearing capacities. For instance, PTFE tubing can usually withstand higher pressures than PVC tubing.
- Chemical Compatibility: The tubing must not react with the fluids it transports. Otherwise, it could contaminate the fluid or be damaged itself.
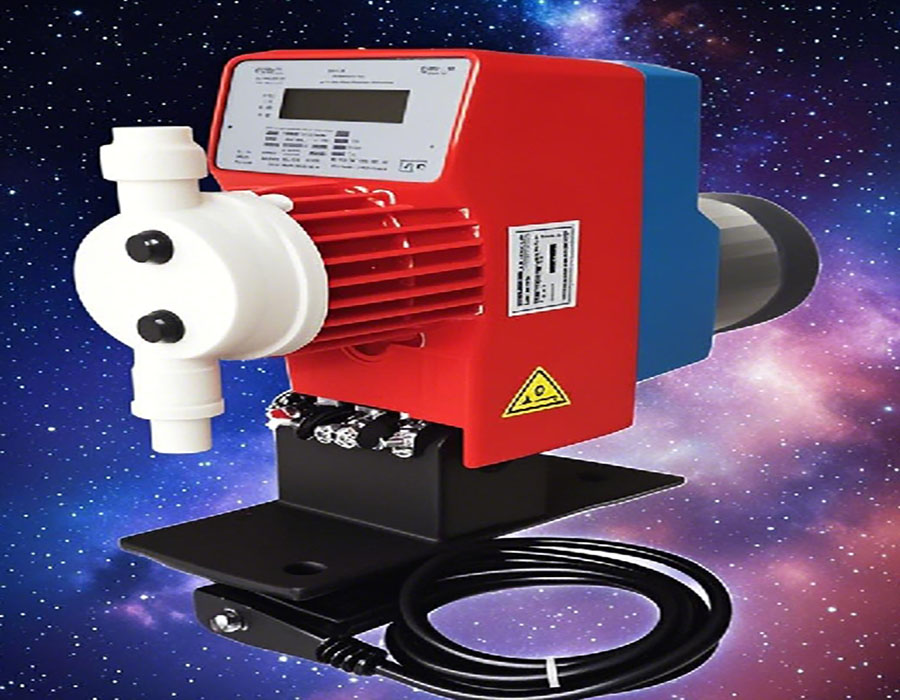
How to Choose the Right Dosing Pump Tubing
Consider the Fluid Type
- Corrosive Fluids: If you’re dealing with corrosive chemicals like strong acids or alkalis, PTFE tubing is a better choice. For example, in a chemical manufacturing plant producing hydrochloric acid, PTFE tubing can ensure safe transportation.
- Food – Grade Fluids: When transporting food – grade liquids, silicone tubing is preferred due to its non – toxicity and compliance with food safety standards.
Analyze the Working Conditions
- Temperature: High – temperature environments require tubing with high – temperature resistance, such as PTFE. In contrast, PVC tubing may deform or degrade at high temperatures.
- Pressure: Determine the maximum pressure the tubing will be subjected to. Choose tubing with a pressure – rating higher than the operating pressure to avoid burst or leakage.
Cost – Benefit Analysis
Compare the costs of different tubing materials. While PTFE is more expensive, it may be more cost – effective in the long run for applications with high – demand for chemical resistance and durability. However, for low – cost and less – demanding applications, PVC tubing can be a suitable option.
Comparison between Different Dosing Pump Tubing Materials
Comparison Items | PVC Tubing | PTFE Tubing | Silicone Tubing |
Cost | Low | High | Medium |
Chemical Resistance | Good for common chemicals | Excellent for a wide range of chemicals | Good for certain chemicals |
Temperature Resistance | Limited (usually up to 60 – 80°C) | High (can withstand up to 260°C) | Moderate (up to 150°C) |
Flexibility | Moderate | Low | High |
As shown in the table, each tubing material has its own advantages and disadvantages. It’s important to choose the right one based on your specific needs.
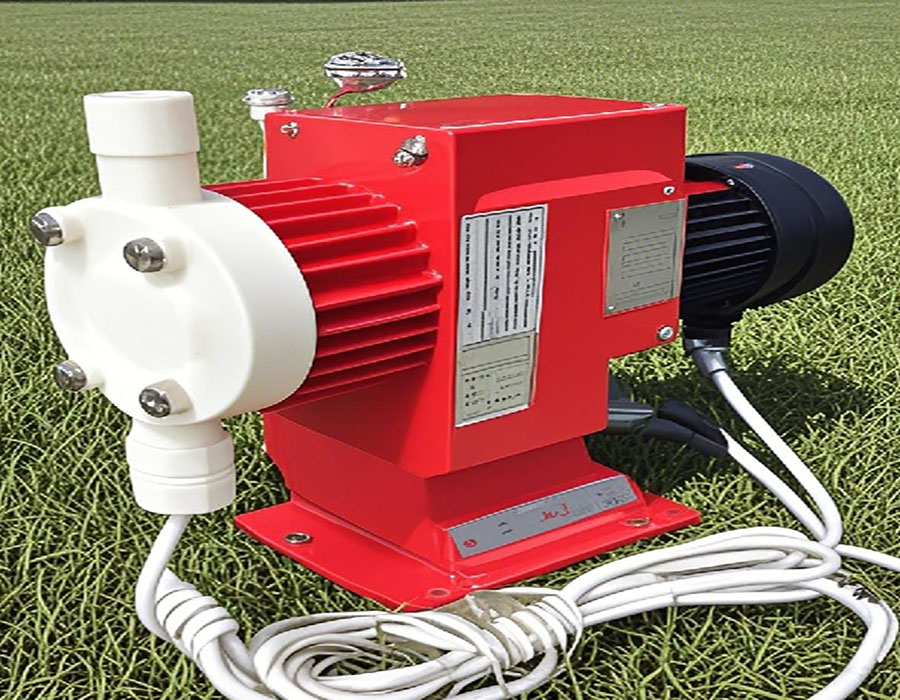
Common Problems with Dosing Pump Tubing and Solutions
Leakage
Problem: Leakage can occur at the tubing joints or due to tubing damage. This can lead to fluid loss and potential safety hazards.
Solution: Check the tubing joints regularly. Use proper connectors and sealing materials. If the tubing is damaged, replace it immediately.
Blockage
Problem: Particles in the fluid or solidified substances can block the dosing pump tubing, affecting the flow rate and dosing accuracy.
Solution: Install filters before the tubing to prevent particles from entering. Clean the tubing regularly, especially when using fluids that are prone to solidification.
Chemical Degradation
Problem: Some fluids may react with the tubing material over time, causing degradation and reduced performance.
Solution: Select tubing with high chemical compatibility. Monitor the tubing for signs of degradation and replace it when necessary.
Case Sharing: What We Found in a 2024 Project
Our team worked with a food – processing company in 2024. They were using PVC tubing in their dosing system for adding flavorings to beverages. However, after a few months, the tubing started to degrade due to the acidic nature of the flavorings. After switching to silicone tubing, the problem was solved. The production efficiency increased by 20%[1] as there were no more blockages or leaks.
Installation and Maintenance Guide for Dosing Pump Tubing
Installation Steps
- Measure and cut the tubing to the appropriate length. Use a sharp cutter to ensure a clean cut.
- Connect the tubing to the pump and other components. Make sure the connections are tight using appropriate fittings.
- Check for any kinks or bends in the tubing. Straighten the tubing to ensure smooth flow.
- Secure the tubing in place using clamps or brackets to prevent movement.
- Conduct a pressure test to check for leaks before starting the operation.
Maintenance Tips
- Regularly inspect the tubing for signs of wear, damage, or leakage.
- Clean the tubing and filters regularly to prevent blockage.
- Replace the tubing according to the manufacturer’s recommendations or when it shows signs of degradation.
Common Mistakes in Using Dosing Pump Tubing ⚠Attention:
- Wrong Material Selection: Choosing the wrong tubing material can lead to premature failure. For example, using PVC tubing for high – temperature applications will cause it to deform.
- Improper Installation: Incorrect installation, such as loose connections, can result in leakage. Make sure to follow the installation instructions carefully.
- Neglecting Maintenance: Lack of regular maintenance can lead to blockages and reduced tubing lifespan. Set up a maintenance schedule and stick to it.
Summary: Practical Operation Checklist
- Select the right tubing material based on fluid type and working conditions.
- Ensure proper installation with tight connections and no kinks.
- Regularly inspect the tubing for damage, leakage, and blockage.
- Clean the tubing and filters regularly.
- Replace the tubing in a timely manner when necessary.
In conclusion, dosing pump tubing is an essential part of any dosing system. By understanding its types, choosing the right one, and maintaining it properly, you can ensure the smooth operation of your dosing system and achieve accurate dosing results.