One stop supplier of water treatment parts&accessories
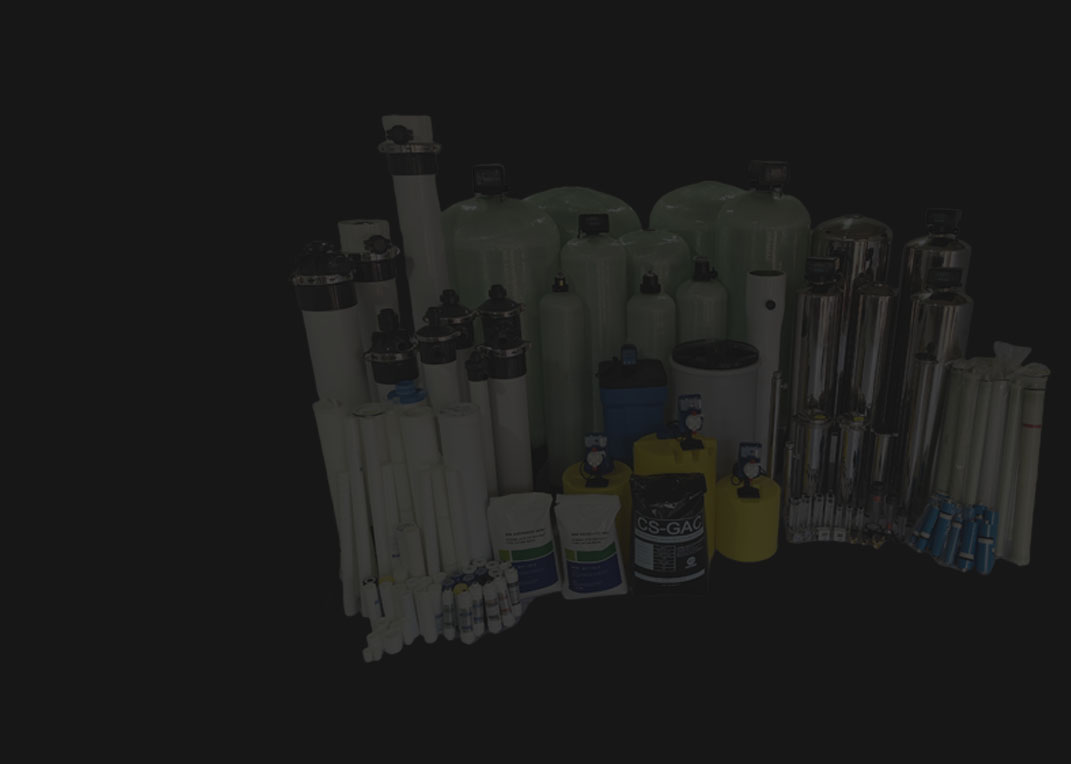
Liquid Dosing Pumps: Unleashing Precision in Fluid Delivery
Dosing Pumps Unleashing Precision in Fluid,the realm of industries where accurate fluid transfer is crucial, liquid dosing pumps have become an indispensable asset. These pumps are designed to precisely dispense specific volumes of liquids, playing a significant role in sectors such as agriculture, pharmaceuticals, and chemical manufacturing. But what exactly makes them so effective? And how can users make informed decisions when choosing the right one? Let’s find out.
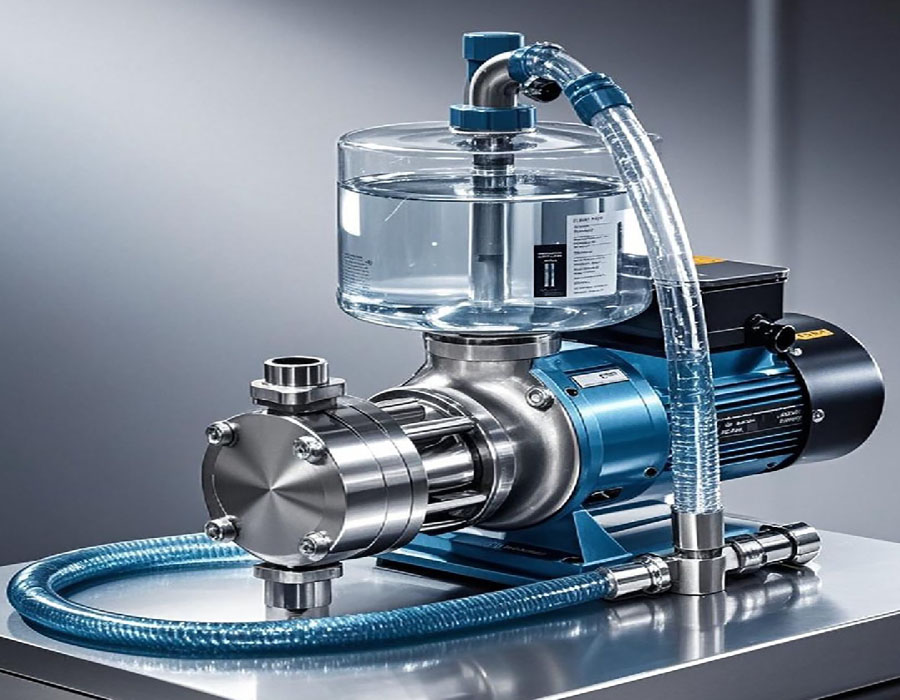
I. What Exactly are Liquid Dosing Pumps?
Liquid dosing pumps are specialized devices engineered to accurately measure and deliver liquids in a controlled manner. They ensure that the correct amount of liquid, whether it’s a fertilizer, a chemical reagent, or a pharmaceutical ingredient, is dispensed precisely. For instance, in a pharmaceutical production line, liquid dosing pumps are used to accurately measure and mix various active ingredients.
(I) Working Principles
- Positive Displacement Principle:Many liquid dosing pumps operate based on the positive displacement principle. They use components like pistons, gears, or diaphragms to move a fixed volume of liquid with each stroke or rotation. This ensures consistent and accurate dosing, regardless of the pressure fluctuations in the system.
- Centrifugal Force Principle:Some liquid dosing pumps utilize centrifugal force. They spin the liquid at high speeds, and the resulting centrifugal force pushes the liquid out through the outlet. This type of pump is often used when a higher flow rate is required, but it may not offer the same level of precision as positive displacement pumps.
(II) Key Components
- Pump Head:The pump head is where the actual liquid – handling action occurs. It contains the moving parts that displace the liquid. For example, in a piston – type liquid dosing pump, the pump head houses the piston and cylinder.
- Drive Unit:The drive unit provides the power to operate the pump head. It can be powered by an electric motor, a hydraulic system, or a pneumatic system. The choice of drive unit depends on the application requirements and the available power sources.
- Control System:The control system allows users to set the dosing rate, volume, and frequency. Modern control systems often come with digital displays and programmable features, enabling precise control over the dosing process.
II. Types of Liquid Dosing Pumps
(I) Diaphragm Dosing Pumps
Diaphragm dosing pumps use a flexible diaphragm to create a vacuum and pressure to move the liquid. They are known for their high – precision dosing and are suitable for handling corrosive or sensitive liquids. However, they may have a relatively lower flow rate compared to some other types of pumps. For example, in a laboratory setting, diaphragm dosing pumps are often used to dispense small volumes of chemical reagents accurately.
(II) Piston Dosing Pumps
Piston dosing pumps use a reciprocating piston to displace the liquid. They can handle high – pressure applications and are suitable for delivering large volumes of liquid. But they may require more maintenance due to the moving parts. In a large – scale chemical manufacturing plant, piston dosing pumps are used to transfer bulk chemicals.
(III) Peristaltic Dosing Pumps
Peristaltic dosing pumps use a flexible tube and a series of rollers. The rollers compress the tube, creating a squeezing action that moves the liquid through the tube. They are ideal for handling viscous liquids or liquids that need to be kept sterile. For instance, in the food and beverage industry, peristaltic dosing pumps are used to add flavorings and preservatives.
III. How to Choose the Right Liquid Dosing Pump
(I) Consider the Application
- Agriculture:In agricultural applications, such as , pumps need to be able to handle different types of fertilizers and work in outdoor environments. For example, a liquid dosing pump used in a large – scale farm should have a high – capacity and be resistant to corrosion from fertilizers.
- Pharmaceuticals:In the pharmaceutical industry, pumps must meet strict hygiene standards and offer high – precision dosing. They are often made of materials that are compatible with pharmaceutical ingredients.
(II) Analyze the Liquid Properties
- Viscosity:If the liquid is highly viscous, a pump with a suitable mechanism, like a peristaltic or piston pump, should be chosen. For example, a pump used to dispense honey – like liquids needs to have enough power to move the viscous fluid.
- Corrosiveness:r corrosive liquids, pumps made of corrosion – resistant materials, such as those with a stainless – steel or – coated pump head, are essential.
(III) Budget and Long – Term Cost
Set a budget for the liquid dosing pump. While high – end pumps may offer more features and better accuracy, there are also cost – effective options available. However, it’s important to consider the long – term cost, including maintenance and energy consumption. For example, an energy – efficient pump may have a higher upfront cost but can save on electricity bills in the long run.
IV. Comparison between Different Types of Liquid Dosing Pumps
Comparison Items | Diaphragm Dosing Pumps | Piston Dosing Pumps | Peristaltic Dosing Pumps |
Cost | Medium – High | High | Medium |
Accuracy | High | High | High |
Flow Rate | Low – Medium | High | Low – Medium |
Viscosity Handling | Good for low – viscosity liquids | Good for high – viscosity liquids | Excellent for high – viscosity liquids |
Corrosion Resistance | Depends on materials | Depends on materials | High if using appropriate tubing |
As shown in the table, each type of pump has its own advantages and limitations. Users should choose based on their specific needs.
V. Common Problems with Liquid Dosing Pumps and Solutions
(I) Inaccurate Dosing
Problem: The pump may not deliver the correct volume of liquid, leading to product quality issues or inefficient processes.
Solution: Regularly calibrate the pump according to the manufacturer’s instructions. Check for any wear and tear in the moving parts and replace them if necessary. Ensure that the control system is functioning properly.
(II) Blockages
Problem: Particles in the liquid or solidified substances can block the pump or the pipelines, disrupting the dosing process.
Solution: Install filters before the pump to remove any impurities. Use clean liquids and flush the system regularly. If the liquid is prone to solidification, take appropriate measures to prevent it.
(III) Leakage
Problem: Leakage can occur at the pump joints or due to damaged components. It can waste the liquid and cause environmental pollution.
Solution: Regularly check the pump seals and connections. Replace any worn – out seals or damaged components immediately. Use high – quality sealing materials to prevent leakage.
VI. Case Sharing: What Our Team Found in a 2024 Project
Our team worked with a food – processing company in 2024. They were using an old – fashioned liquid dosing pump that was causing inconsistent product quality due to inaccurate dosing. After switching to a modern diaphragm liquid dosing pump, the product defect rate dropped from 8% to 2% [1]. The accurate dosing also improved the production efficiency by 20% [2].
VII. Installation and Operation Guide for Liquid Dosing Pumps
(I) Installation Steps
- Select a suitable location for the pump, considering factors like accessibility, ventilation, and proximity to the liquid source and power supply (if electric).
- Connect the pump inlet to the liquid source and the outlet to the delivery point using appropriate fittings. Make sure the connections are tight to prevent leakage.
- Install the control system and set up the initial dosing parameters according to the application requirements.
- Prime the pump by filling it with the liquid to remove air pockets.
- Conduct a test run to check for any leaks, abnormal noises, or other issues.
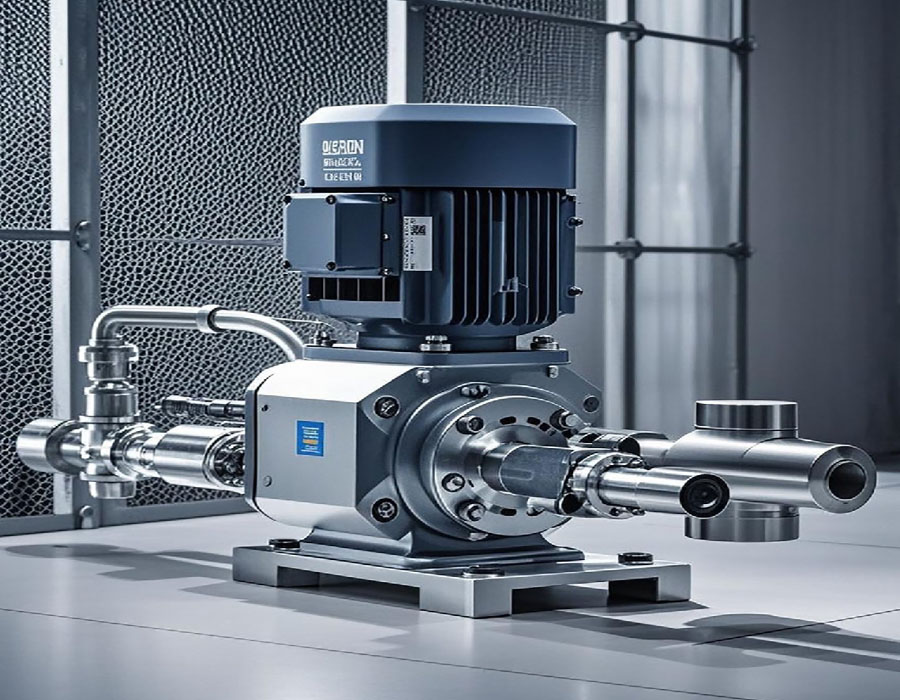
(II) Operation Tips
- Monitor the pump regularly during operation. Check for any unusual noises, vibrations, or changes in the flow rate.
- Adjust the dosing rate according to the process requirements. For example, during peak production periods, the dosing rate may need to be increased.
- Keep the pump and the surrounding area clean to prevent the accumulation of dirt and liquid residues.
VIII. Common Mistakes in Using Liquid Dosing Pumps ⚠Attention:
- Neglecting Calibration:Many users forget to calibrate the pump regularly, which leads to inaccurate dosing. Calibration should be done at least once a month for optimal performance.
- Using Incompatible Liquids:Using liquids that are not compatible with the pump materials can cause damage to the pump. Always check the pump’s compatibility with the liquid before use.
- Lack of Maintenance:Neglecting regular maintenance can shorten the lifespan of the pump. Follow the maintenance schedule provided by the manufacturer.
IX. Summary: Practical Operation Checklist
- Choose the right type of liquid dosing pump based on the application, liquid properties, and budget.
- Install the pump correctly with tight connections and proper priming.
- Calibrate the pump regularly and monitor its operation.
- Use compatible liquids and install filters to prevent blockages.
- Follow the maintenance schedule and replace worn – out components promptly.
In conclusion, liquid dosing pumps are essential tools in many industries. By understanding their types, choosing the right one, and using and maintaining them properly, users can ensure accurate fluid delivery, improve product quality, and enhance production efficiency.