One stop supplier of water treatment parts&accessories
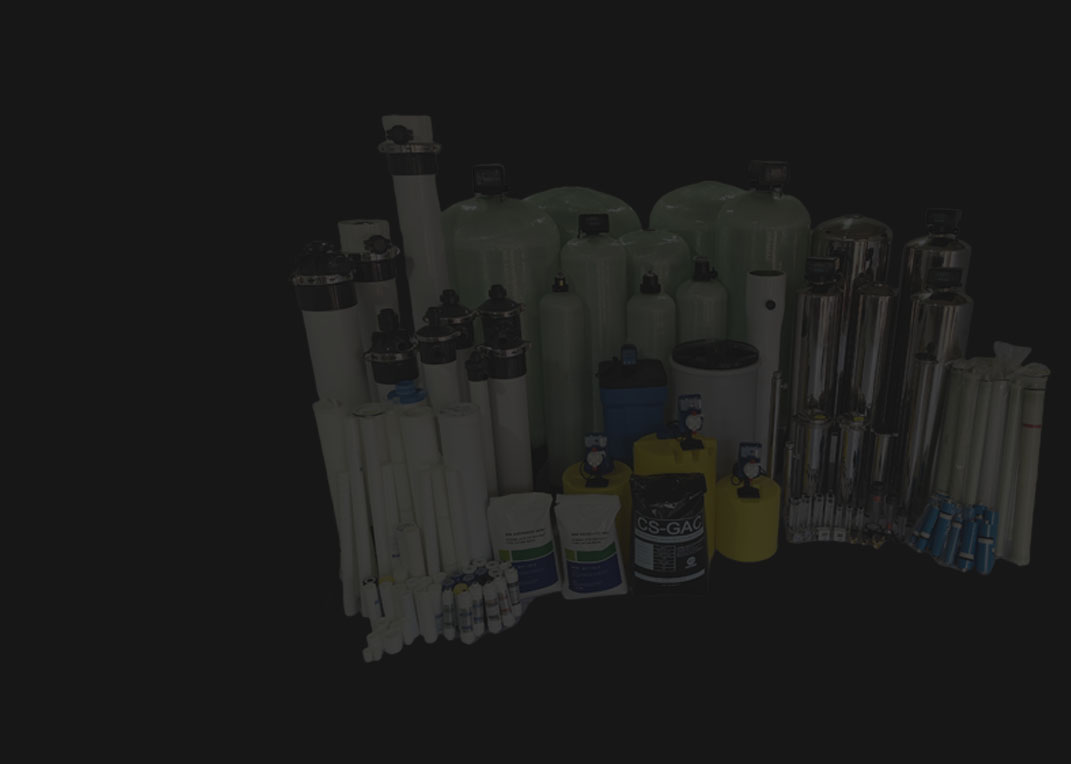
The Indispensable Duo: pH Controller and Dosing Pump
In industrial processes, water treatment, and scientific research, the combination of a pH controller and dosing pump is crucial. This article explores the significance, functionality, and applications of this powerful pair, and how they work together to ensure optimal results in various settings.
1. Introduction to pH Controller and Dosing Pump
A pH controller measures the hydrogen – ion concentration in a solution, giving a numerical value that shows the solution’s acidity or alkalinity. It has a sensor, usually a glass electrode, highly sensitive to pH changes. The sensor sends signals to the controller unit. The unit processes the data and can trigger certain actions based on pre – set pH values.
A dosing pump accurately dispenses a specific volume of liquid, often a chemical solution. Pumps come in types like diaphragm pumps, piston pumps, and peristaltic pumps. Each type has its own advantages in flow rate accuracy, pressure capabilities, and chemical compatibility. When paired with a pH controller, a dosing pump becomes essential for maintaining the desired pH level in a system.
For example, in a water treatment plant, the incoming water’s pH may vary. If it’s too acidic or alkaline, it can cause pipe corrosion or ineffective disinfection. The pH controller monitors the water’s pH constantly. When the pH deviates from the set point, it signals the dosing pump to add the right chemical (acid or base) to bring the pH back to the desired range. This shows their collaborative role in a practical application.

2. Working Principle of pH Controller and Dosing Pump
2.1 pH Controller
The pH controller works on the principle of electrochemistry. The glass electrode in the pH sensor has a special glass membrane. When it contacts a solution, it develops an electrical potential difference related to the hydrogen – ion concentration. The controller measures this difference and converts it into a pH value, then displays it on the screen.
Most modern pH controllers can set upper and lower pH limits. When the measured pH goes beyond these limits, the controller can send out control signals. These signals, often in the form of relays, can switch on or off external devices like a dosing pump.
2.2 Dosing Pump
Dosing pumps work based on different mechanisms. Diaphragm dosing pumps use a flexible diaphragm that moves back and forth. When it moves, it creates a vacuum to draw in liquid on the suction side and then forces it out on the discharge side. Piston dosing pumps use a reciprocating piston to move the liquid. The piston moves in a cylinder, and we can adjust the volume of liquid displaced per stroke to control the dosing rate.
Peristaltic dosing pumps operate by squeezing a flexible tube between a set of rollers. As the rollers rotate, they create contractions and expansions in the tube, propelling the liquid through. Peristaltic pumps are great for handling corrosive or sensitive fluids because the liquid never touches the moving parts.
When integrated with a pH controller, the dosing pump gets a signal from the controller. If the pH is too high, the controller tells the dosing pump to add an acidic solution. If the pH is too low, the dosing pump adds a basic solution. This shows how their working principles are intertwined.
3. Applications of pH Controller and Dosing Pump
3.1 Water Treatment
Water treatment plants widely use pH controllers and dosing pumps. Municipal water treatment facilities must ensure the water for consumers has a pH between 6.5 – 8.5. If the source water’s pH is outside this range, the pH controller and dosing pump work together to adjust it.
For instance, if the source water is acidic due to natural acids or industrial pollutants, the dosing pump adds a base like sodium hydroxide or lime to raise the pH. If the water is too alkaline, it adds an acid like sulfuric acid. This adjustment is crucial for consumer safety and to prevent damage to the water distribution system.
3.2 Industrial Processes
Many industrial processes need precise pH control. In the chemical industry, various chemical reactions require specific pH conditions to work efficiently. We use a pH controller and dosing pump to maintain the right pH during these reactions. In pharmaceutical production, the pH of the reaction medium affects the product’s quality and yield. A small pH deviation can lead to impurities or a lower – than – expected yield.
In the food and beverage industry, pH control is also important. For example, in dairy product production, we need to monitor and adjust the milk’s pH during processing. We can use a pH controller and dosing pump to add substances like citric acid or sodium bicarbonate to reach the desired pH for cheese – making or yogurt production. This highlights their importance across different industries.
3.3 Aquaculture
In aquaculture, maintaining good water quality is essential for the health and growth of fish and other aquatic organisms. The water’s pH in fish tanks or ponds can significantly impact aquatic life. We use a pH controller and dosing pump to keep the water pH within the optimal range for the cultured species.
Most fish species do well in a pH range of 6.5 – 8.0. If the pH drops too low, it stresses the fish and makes them more prone to diseases. If it rises too high, it’s also harmful. The pH controller monitors the water pH continuously, and when needed, the dosing pump adds the right chemicals to correct the pH.
4. Selection and Installation of pH Controller and Dosing Pump
4.1 Selection
When choosing a pH controller, consider several factors. The accuracy of pH measurement is crucial. High – precision pH controllers can measure pH with an accuracy of ±0.01 pH units or better. The controller’s response time is also important, especially in applications where rapid pH changes need detection and correction.
For the dosing pump, factors like required flow rate, pressure capabilities, and chemical compatibility are key. The dosing pump’s flow rate should be enough to add the required chemical amount within a reasonable time. The pump’s materials should resist the chemicals it will handle to prevent corrosion and ensure a long service life.
4.2 Installation
Installing a pH controller and dosing pump needs careful planning. Place the pH sensor in a location where it can accurately measure the solution’s pH. Put it in a well – mixed area, away from turbulence or chemical interference.
Install the dosing pump close to the chemical addition point. Properly size and connect the pump’s suction and discharge lines to prevent leaks and ensure smooth operation. Make the electrical connections for both the pH controller and dosing pump according to the manufacturer’s instructions for safety and proper functioning. This shows their selection and installation, which is practical for users.
5. Maintenance and Troubleshooting of pH Controller and Dosing Pump
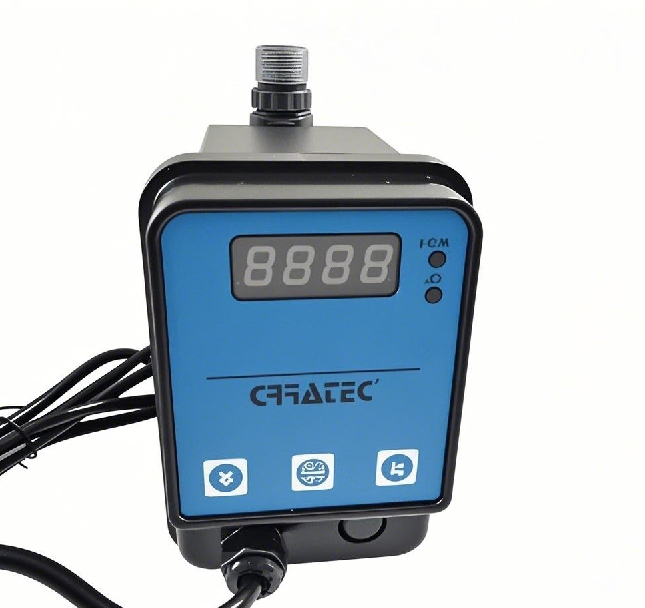
5.1 Maintenance
Regular maintenance is essential for the reliable operation of the pH controller and dosing pump. Calibrate the pH sensor regularly. Calibration means exposing the sensor to solutions of known pH values and adjusting the controller to match the correct readings. This helps maintain the pH measurement’s accuracy.
For the dosing pump, inspect and replace the seals, diaphragms (if it’s a diaphragm pump), and other moving parts as needed. Lubricate the pump according to the manufacturer’s recommendations. Also, regularly check the chemical lines for signs of corrosion or blockage.
5.2 Troubleshooting
If the pH controller shows inaccurate readings, a dirty or damaged sensor may cause it. Cleaning or replacing the sensor may solve the problem. If the dosing pump doesn’t deliver the correct chemical amount, a clogged suction line, a worn – out diaphragm, or a malfunctioning control signal from the pH controller could be the cause. Checking and repairing these components can fix the issue. This focuses on their maintenance and troubleshooting, important for their long – term performance.
6. Future Developments and Trends
The field of pH control and dosing technology is always evolving. Developers are creating newer pH sensors with improved accuracy, longer lifespan, and better resistance to harsh environments. For example, some sensors now use advanced nanomaterials to enhance sensitivity and stability.
Dosing pumps are also getting more intelligent, with features like variable – speed drives and remote monitoring capabilities. These advancements enable more precise dosing control and better integration with overall process control systems. In the future, we can expect even more seamless integration between pH controllers and dosing pumps, along with the development of more advanced control algorithms that can adapt to complex and dynamic process conditions. This looks ahead to future trends, emphasizing their continuous development.
In conclusion, the pH controller and dosing pump are integral components in many applications. Their ability to work together to maintain the correct pH level in various solutions is essential for the success of industrial, environmental, and scientific processes. By understanding their working principles, applications, selection criteria, installation requirements, maintenance needs, and future trends, users can make the most of this powerful duo. Whether it’s ensuring clean water for a community, producing high – quality industrial products, or maintaining a healthy aquatic environment, the pH controller and dosing pump play a vital role. So, for anyone involved in processes that need pH control, understanding these two devices well is crucial.