One stop supplier of water treatment parts&accessories
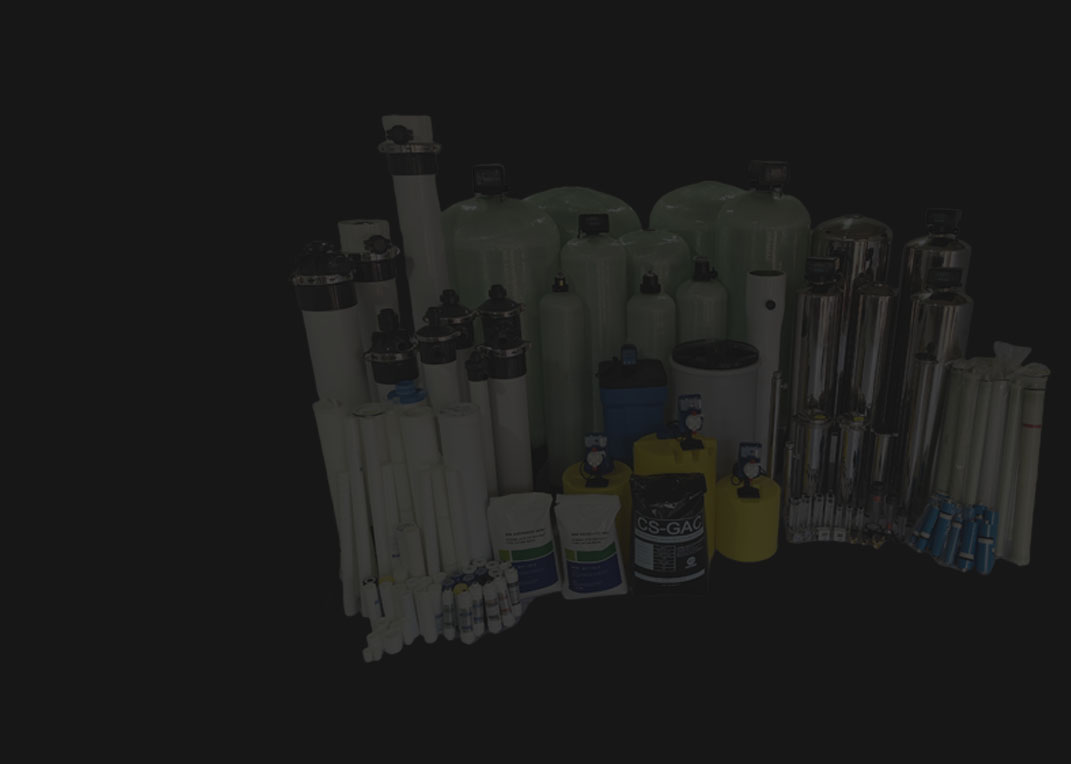
Chemical dosing pump kamoer Dosing System Electric Liquid Dosing electromagnetic diaphragm pump
PRODUCT PARAMETERS
- Product Name: Dosing Pump
- Power Supply: 100-240 Vac50/60 Hz
- Diaphragm Material: PTFE
- Structure: Diaphragm Pump
- Power: Electric
- Application: Metering
- Use:Accurate control and delivery of liquid chemical agents
- Packing: Standard Exportation Package
Description
Chemical Dosing Pump: Precision and Efficiency in Fluid Management
In industries ranging from water treatment to manufacturing, chemical dosing pumps play a vital role in ensuring accurate and efficient delivery of chemicals. Precise amounts of chemicals are designed to be handled by these specialized pumps, which makes them indispensable for processes that require consistency and reliability.
What is a Chemical Dosing Pump?
Manufacturers design a chemical dosing pump to inject precise amounts of chemicals into a fluid stream, tank, or pipeline. They make these pumps handle a wide range of chemicals, including acids, alkalis, disinfectants, and coagulants, to ensure accurate dosing for optimal results.
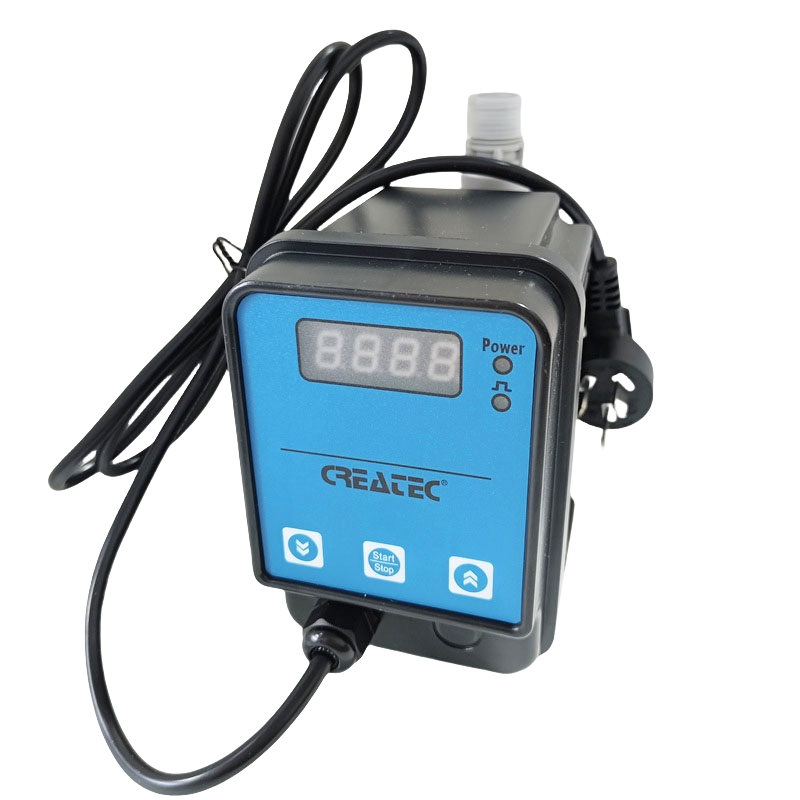
Parameters of metering pump
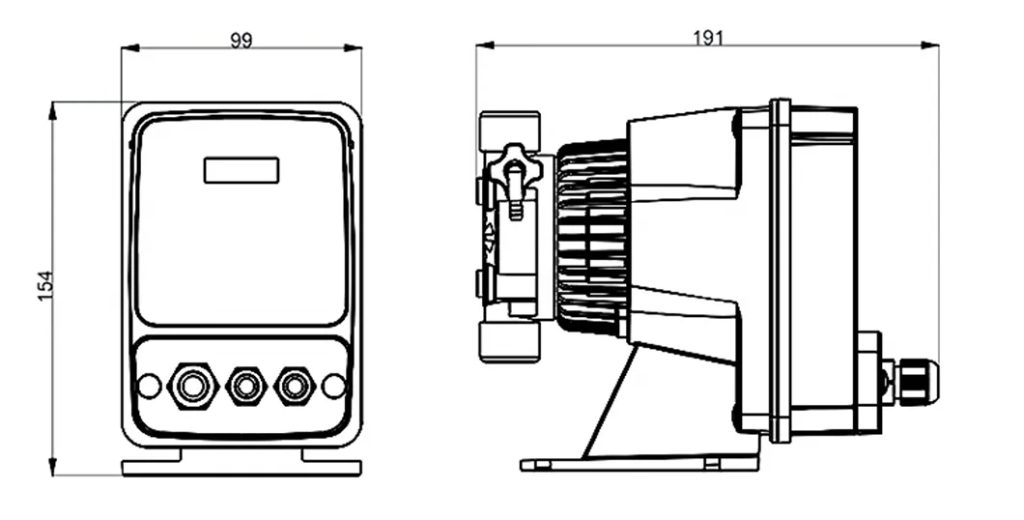
Technical parameter list

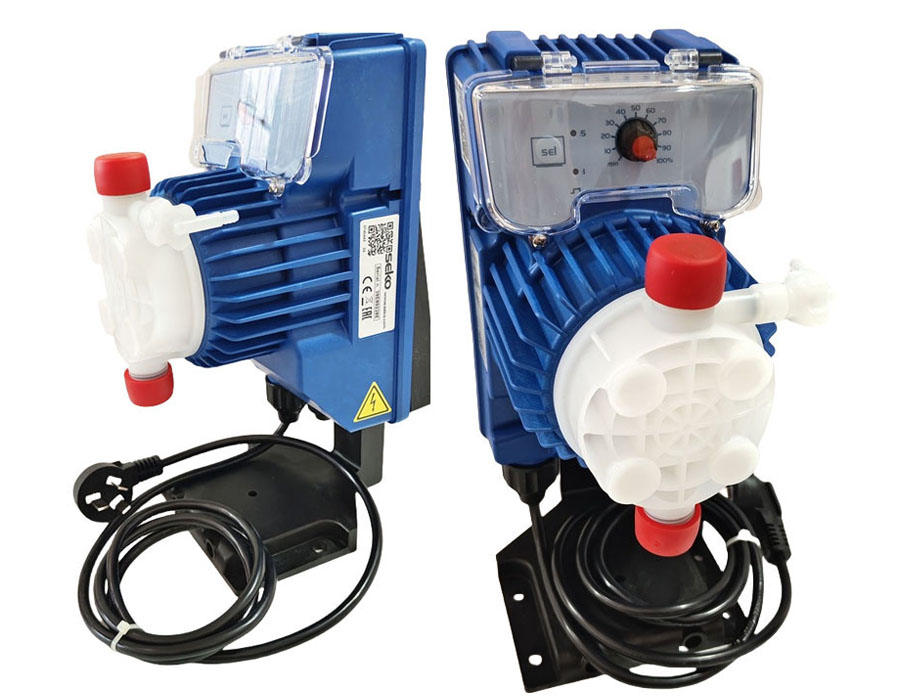
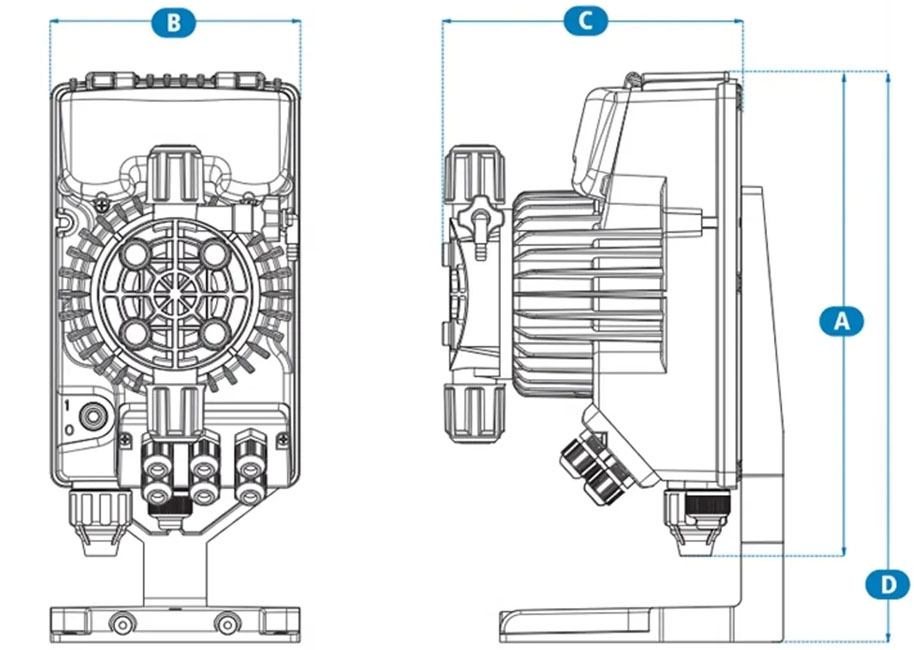
Technical parameter list(chemical dosing pump)
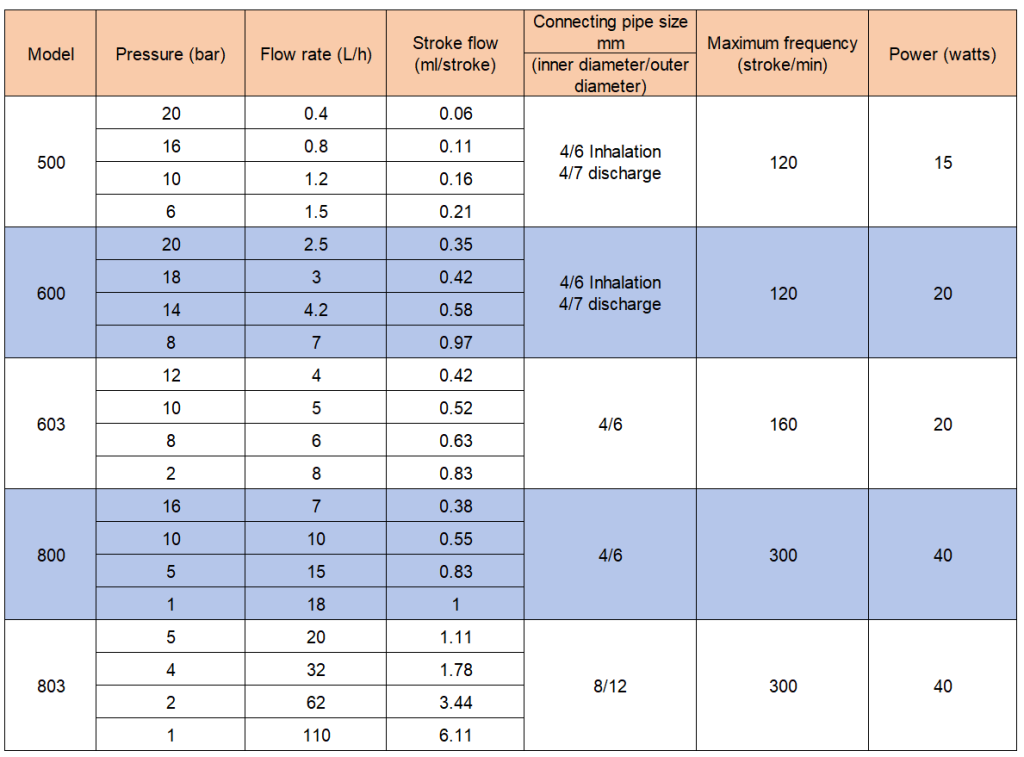
Key Benefits of Chemical Dosing Pump
Enhanced Precision and Accuracy in Chemical Delivery
First and foremost, precision and accuracy are the cornerstones of chemical dosing pumps. These pumps are capable of delivering exact amounts of chemicals, which is crucial for ensuring consistent results across different processes.
Moreover, this high – level of precision significantly minimizes waste, making the overall operation more resource – efficient.
Secondly, the versatility of these pumps is remarkable. They can handle a wide range of chemicals, including corrosive, viscous, and hazardous substances. This means that these pumps can effectively perform the task of dosing regardless of the nature of the chemicals, which expands their application scope in various industries.
In addition, improved efficiency is another key advantage. By automating the dosing process, chemical dosing pumps reduce the need for manual labor. This not only saves time but also greatly reduces the likelihood of human error, thereby enhancing the overall operational efficiency.
Furthermore, cost – effectiveness is a significant benefit. Thanks to precise dosing, we can minimize the usage of chemicals. As a result, we can reduce operational costs and, at the same time, lessen the environmental impact, making it a sustainable choice.
Moreover, durability is an important characteristic. Manufacturers construct chemical dosing pump from robust materials such as stainless steel, PVC, and PTFE. These materials enable the pumps to withstand harsh conditions, ensuring a long service life and reliable performance.
Finally, safety is a top priority. These pumps are designed in a way that reduces the risk of chemical spills and exposure. By doing so, they create a safer working environment for operators, protecting both human health and the surrounding environment.
How Does a Chemical Dosing Pump Work?
Working Process of Chemical Dosing Pumps
First of all, the suction phase is the initial step in the operation of a chemical dosing pump. During this phase, the pump draws a specific volume of chemical from a storage tank. This is the fundamental process that prepares the chemical for subsequent dosing.
Next, comes the dosing phase. In this stage, the chemical is injected into the target system at a controlled rate. This controlled injection ensures that the right amount of chemical is introduced into the system, which is crucial for achieving the desired results.
Moreover, an important feature of most dosing pumps is the adjustable flow rate. This means that users can adjust the flow rate to meet specific requirements. Whether it’s a high – volume or low – volume dosing need, this adjustability provides flexibility in various applications.
Finally, advanced models of dosing pumps offer automated control. We can integrate these models with sensors and controllers for automated dosing based on real – time data. This automation not only enhances the efficiency of the dosing process but also improves the accuracy by responding to the actual conditions in real – time.
Types of Chemical Dosing Pump
Firstly, there are diaphragm pumps. These pumps use a flexible diaphragm to displace chemicals. As a result, they offer high accuracy and reliability, making them a popular choice in many chemical dosing scenarios where precision is key.
Secondly, peristaltic pumps come into play. They utilize rotating rollers to compress a tube. This mechanism makes them ideal for handling abrasive or viscous fluids, as the tube acts as a barrier between the fluid and the pump components, reducing wear and tear.
Next, piston pumps are well – suited for specific situations. They are suitable for high – pressure applications. In such high – pressure environments, piston pumps provide consistent and precise dosing, ensuring that the chemical delivery is both stable and accurate.
Finally, solenoid – driven pumps have their own advantages. They are compact and cost – effective. Due to these characteristics, they are ideal for low – flow applications, where a small, affordable pump can meet the requirements without over – complicating the system.
Choosing the Right Chemical Dosing Pump
When selecting a chemical dosing pump, consider the following factors:
– You should ensure that you select pump materials that are resistant to the chemicals being used.
– Flow Rate and Pressure: Choose a pump that meets your system’s flow rate and pressure requirements.
– Accuracy: Opt for pumps with adjustable settings for precise dosing.
– Automation: Consider models with automation features for integration into control systems.
– Maintenance: Look for pumps with easy-to-replace parts and low maintenance requirements.
Maintenance Tips for Chemical Dosing Pump
First and foremost, regular inspections are of utmost importance. You should check for wear and tear, leaks, or blockages in the pump components. This proactive step allows you to identify potential issues early on and take timely action to prevent more serious problems.
Next, it’s crucial to clean the pump. Flush the pump regularly to prevent chemical buildup and corrosion. By doing so, you can extend the lifespan of the pump and maintain its efficiency.
In addition, replace parts as needed. Over time, components such as diaphragms, tubes, or seals may deteriorate. Replacing them promptly helps maintain the pump’s optimal performance and ensures it operates as intended.
Finally, periodically calibrate the pump. This step is essential to ensure accurate dosing. Precise dosing is vital for the proper functioning of the chemical dosing system, and regular calibration guarantees that the pump delivers the correct amount of chemicals.
FAQs
we offer a comprehensive range of products tailored to meet the diverse needs of the water purification and treatment industry. Our portfolio includes but is not limited to filters and filter media, pump systems, valves and fittings, UV sterilizers, reverse osmosis membranes, water softeners,Precision filters, filter cartridge, Flowmeter and advanced monitoring and control systems. Each product is designed with precision and engineered for durability, ensuring optimal water quality and system efficiency. Whether you’re upgrading an existing facility or building a new one, we have the solutions to fit your specific water treatment requirements.
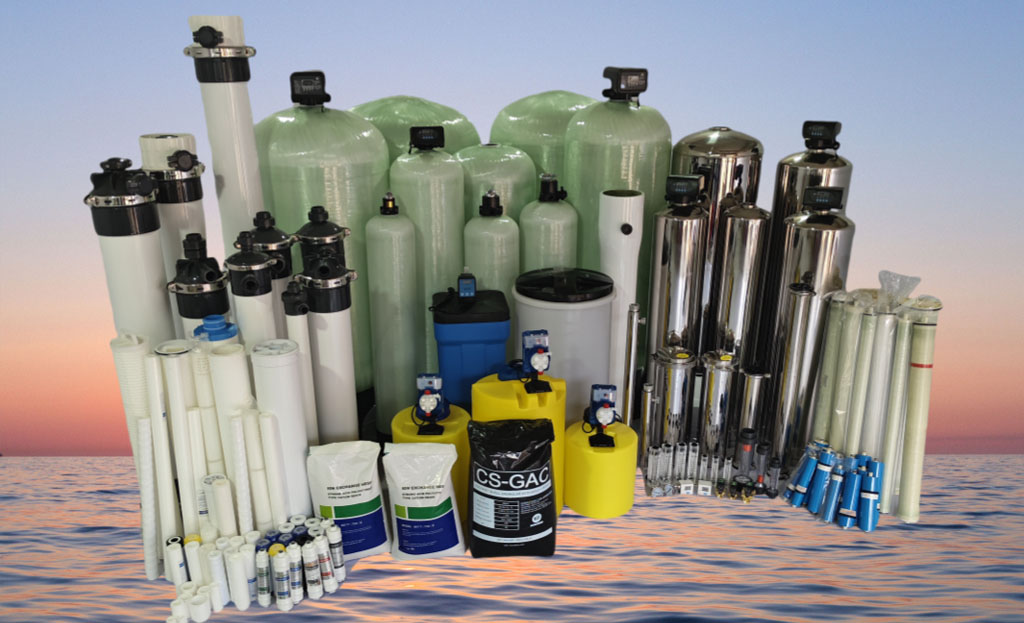
we utilize a robust logistics network to ensure timely and reliable delivery of our products worldwide. We ship through a variety of trusted channels, including air freight, ocean freight, and express couriers, depending on the urgency and destination of the shipment. Our logistics partners are carefully selected for their extensive reach, track record of on-time delivery, and commitment to safety and security. Additionally, we offer flexible shipping options to accommodate different budgets and timelines, ensuring that our customers receive their orders promptly and in perfect condition.
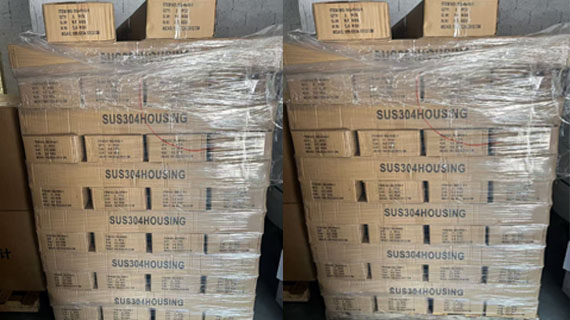
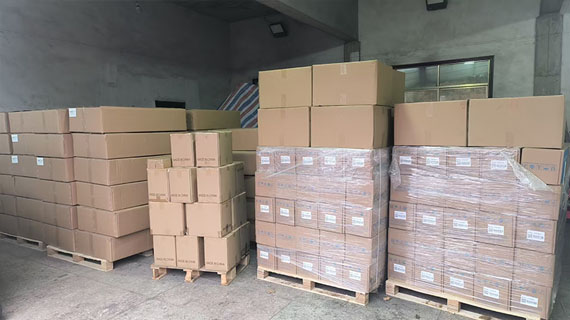
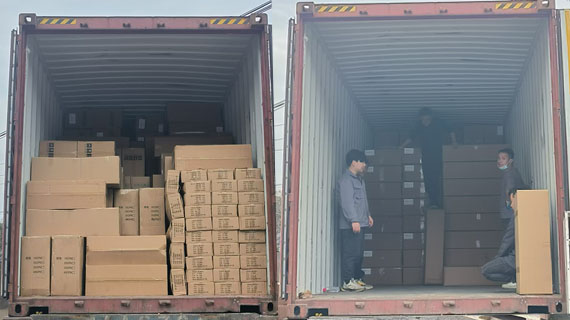
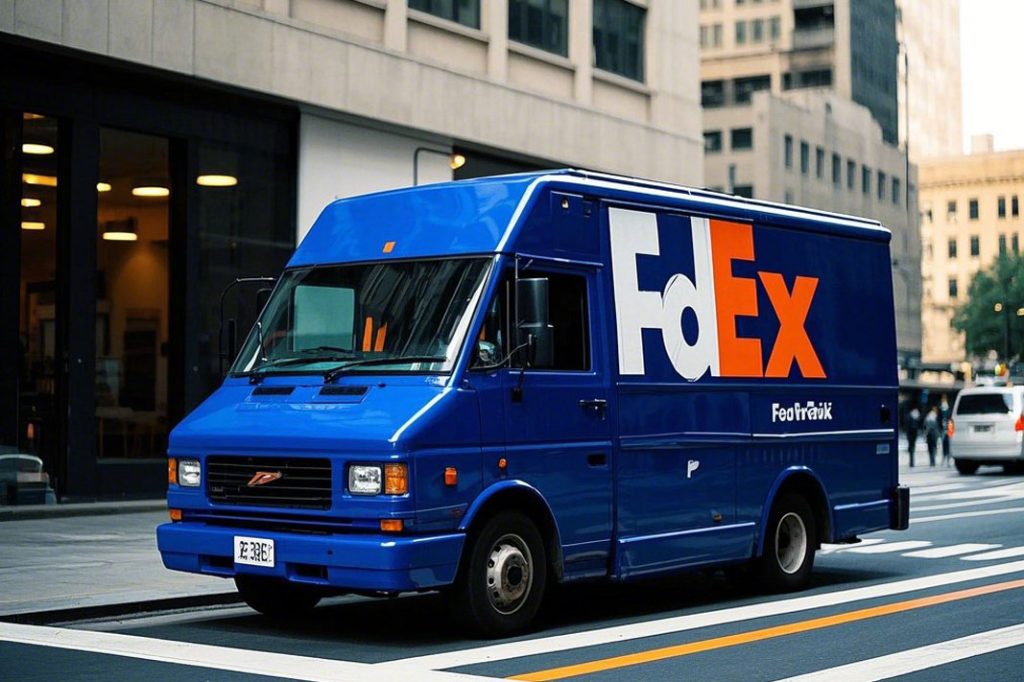
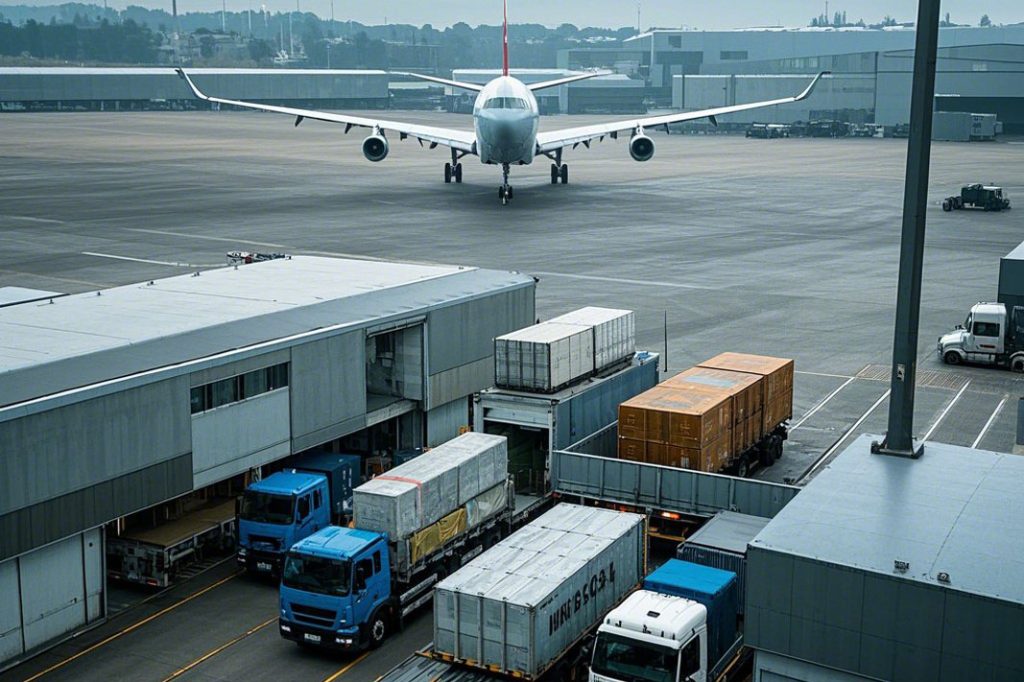
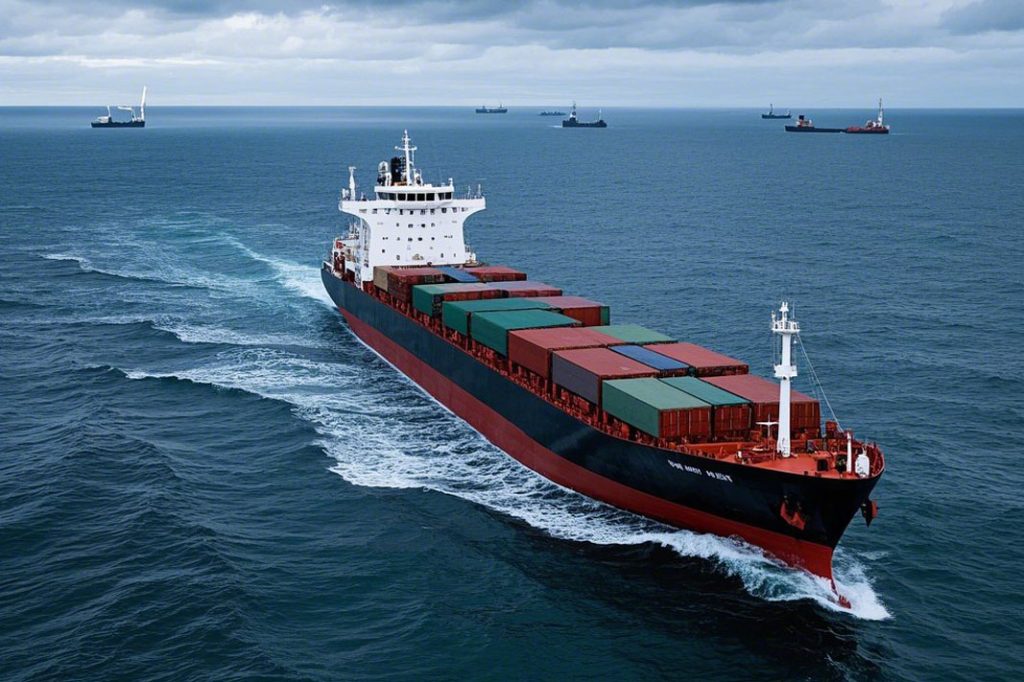
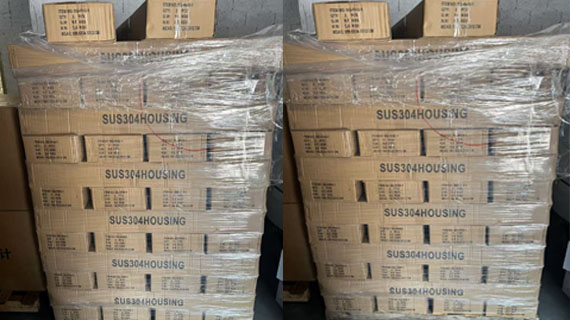
Absolutely, we can customize packaging for your water treatment accessories. We understand the unique needs of each client and offer bespoke packaging solutions that cater to your specific requirements. Whether it’s a matter of size, material, or design, we’ll work closely with you to ensure that your packaging not only protects your products but also reflects your brand identity and meets all your expectations.
Our ordering process for water treatment accessories is designed to be straightforward and efficient. First, you’ll reach out to us with your specific needs, whether it’s for standard products or customized solutions. Our team will then provide you with detailed information, including product specifications, pricing, and availability. Once you’ve decided on the items you wish to order, we’ll guide you through the ordering process, which typically involves confirming your order details, selecting your preferred payment method, and arranging for shipment. Throughout the process, our dedicated customer service team is available to assist you with any questions or concerns, ensuring a seamless and satisfying ordering experience.
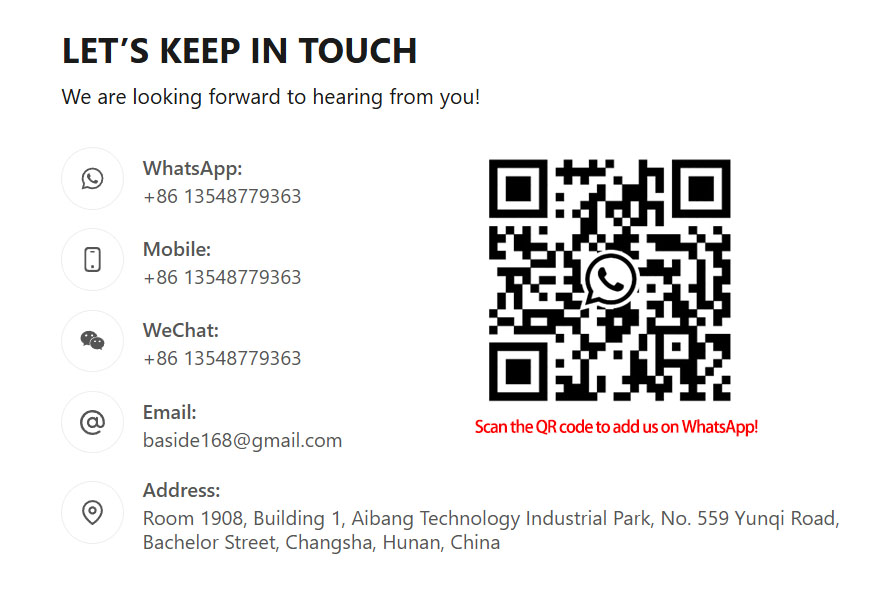
we accept bank transfers, allowing you to make payments directly into our account ,and third-party payment platforms such as PayPal, Western Union, or MoneyGram.We also support payments in multiple currencies to accommodate our clients’ needs. To discuss the most suitable payment method for you, please feel free to contact our customer service team.
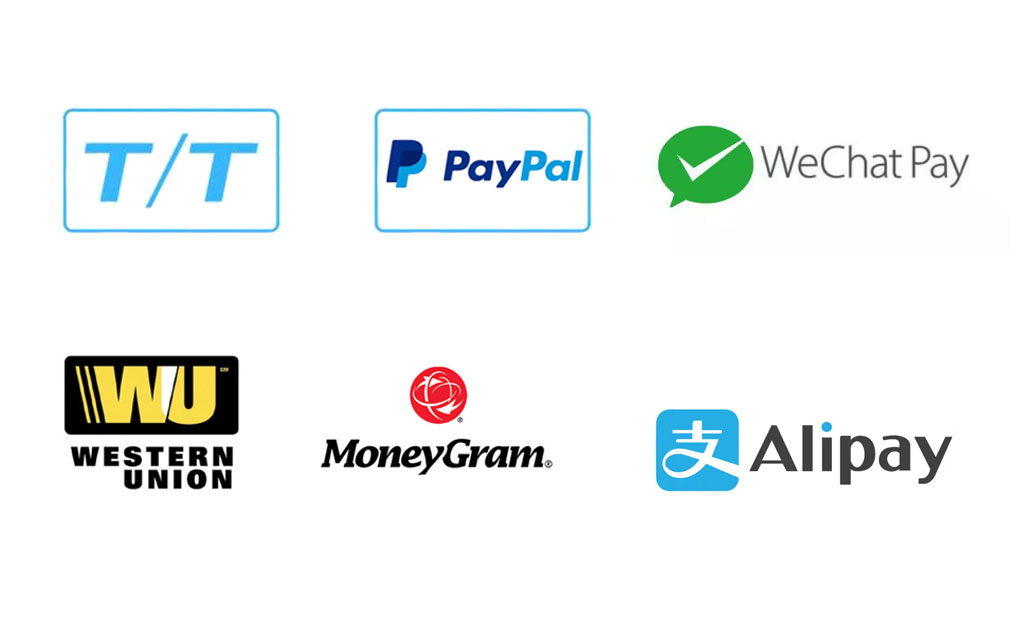